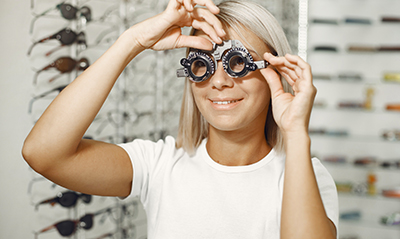
Le plasturgiste qui transforme les matières plastiques pour obtenir un objet fini, en utilisant différents procédés (moulage par injection, extrusion ou soufflage, calandrage pour la fabrication de films et de feuilles ...), est exposé à des risques chimiques. Ces risques chimiques sont induits soit par contact cutané, soit par voie respiratoire par inhalation de poussières ou libération de produits volatils toxiques lors de l’élévation de la température mise en œuvre dans le procédé de fabrication.
Les matières plastiques sont polymérisées par chauffage à partir de molécules monomères et de composants auxiliaires (stabilisateurs, catalyseurs, ...). Le plasturgiste qui transforme ces matières plastiques pour obtenir un objet fini, en utilisant différents procédés (moulage par injection, extrusion ou soufflage, calandrage pour la fabrication de films et de feuilles ...), est ainsi exposé à des risques chimiques.
Ces risques chimiques sont induits soit par contact cutané, soit par voie respiratoire par inhalation de poussières ou libération de produits volatils toxiques lors de l’élévation de la température mise en œuvre dans le procédé de fabrication.
A ces risques chimiques, s’ajoutent des risques liés :
- à la chaleur ambiante des machines, étuves et fours de séchage,
- au bruit et aux vibrations des presses, concasseurs ...et aux ultrasons des soudeuses des thermoplastiques,
- à l’incendie et à l’explosion causés par les poussières électrisées de matières plastiques, ou dus à la présence de solvants lors des opérations de nettoyage des moules, ou de vapeurs inflammables dans les locaux de stockage,
- et à tous les risques physiques de coupures, chutes de plain-pied, électrocution et ceux causés par les manutentions,...
Ces risques chimiques, thermiques, mécaniques, électriques... des ateliers de plasturgie peuvent être maîtrisés par l’utilisation de machines et d’équipements et la présence d’une installation électrique et de protection incendie conformes aux normes, la captation de gaz et de poussières au plus près de leur point d’émission, une ventilation efficace, et par le respect des exigences essentielles de sécurité (lutte contre le bruit, hygiène des locaux...) et de protection individuelle, avec une attention soutenue pendant les périodes de mise en place des outillages et de démarrage de production, ou lors des opérations de maintenance et de réparation.
Les principaux risques dans la plasturgie
Les produits finis en matière plastique sont d’une grande diversité et omniprésents dans tous les objets (tubes et goulottes, bouteilles et emballages, fenêtres et gouttières dans le bâtiment, tableaux de bord et pare-chocs pour l’automobile, boîtiers et enveloppes d’appareils électriques et ménagers, ameublement, articles jetables...), et à chaque type de produit à fabriquer, selon sa taille, sa forme, les qualités recherchées, correspond une matière de base, un adjuvant et une technique de transformation.
Il existe de nombreuses techniques pour fabriquer des objets en matière plastique polymère à partir de matériaux monomères et d’auxiliaires et d’adjuvants (pour renforcer, stabiliser, catalyser...) fournis par l’industrie chimique, et possédant chacun leur propre toxicité.
Il y a deux grandes catégories de matières plastiques :
- Les produits thermoplastiques sont fabriqués à partir de poudres, de granulés, ou de semi-finis en plaques, présentant la caractéristique de fondre par augmentation de la température et de se figer en se refroidissant dans un moule.
La soudure par ultrasons des matières thermoplastiques repose sur l'association d'une pression et d'une vibration ultrasonore.
Cette vibration haute fréquence produit un échauffement important dans la matière et provoque sa fusion.
- Les produits thermodurcissables (ou thermorigides) sont fabriqués à partir de produits partiellement polymérisés dont la mise en forme par polymérisation complète dans le moule s’achève avec l’ajout de catalyseurs.
Il y a donc différentes sortes de risques dans la plasturgie, liés aux produits, aux procédés et aux machines utilisées :
-
Les risques chimiques des plasturgistes
Lors de la transformation des matières plastiques, l’élévation de la température peut entraîner la libération de produits volatils potentiellement dangereux. Par ailleurs, l’exposition des plasturgistes aux poussières de matières plastiques lorsqu’elles utilisées en poudre, lors du mélange et broyage avec leurs adjuvants, ou de poussières de produits riches en colorants (sels de plomb, sulfure de cadmium) génèrent aussi des risques. Des produits de décomposition thermique (émanations et / ou vapeurs) peuvent être émis pendant les opérations de fabrication et de finissage.
L’exposition des plasturgistes à ces poussières et composés gazeux irritants et/ou sensibilisants (aldéhydes et acides formique et acétique, acide chlorhydrique pour les plastiques chlorés ...), à des vapeurs de solvants, génère des risques de réactions allergiques, de troubles respiratoires par inflammation de la muqueuse nasale et bronchique, d’irritation des muqueuses oculaires, de troubles neurologiques pour certains d’entre eux (styrène). Les matières plastiques sont aussi une cause fréquente de dermatoses professionnelles avec des composants irritants et allergènes (monomères, durcisseurs et certains additifs).
La plasturgie utilise différentes matières plastiques, polyéthylène, polypropylène, polychlorure de vinyle (PVC), polystyrène, résines, etc. avec libération possible de monomères ou produits de base résiduels (formol, phénol, isocyanates...).
Les isocyanates, en cas de contact cutané ou d’inhalation, risquent de provoquer des allergies (asthme, eczéma), des pneumopathies d'hypersensibilité, des blépharo-conjonctivites.
De même, le formaldéhyde (formol), est une substance très volatile, très toxique et classé cancérogène avéré. Les résines époxydiques, matières plastiques thermodurcissables, peuvent entrainer des dermatites de contact allergique (eczéma) dues aux substances allergènes qu’elles contiennent.
Une forte dose de chlorure de vinyle inhalée quotidiennement durant de longues années, notamment lors du décroutage des autoclaves après polymérisation sans protection, peut être la cause d'un cancer du foie (angiosarcome hépatique).
Le phtalate DEHP, plastifiant permettant d’augmenter la flexibilité des matières plastiques (PVC souple), est une substance ayant des propriétés toxiques pour la reproduction et suspectée de représenter un risque chez la travailleuse enceinte.
Les défauts d’emballage (sacs détériorés...) participent à l’émission de vapeurs toxiques pendant les périodes de transvasement et de stockage.
Enfin, les composés organiques volatils halogénés de dégraissage et de décapage (dichlorométhane, trichloroéthylène), utilisés lors de la maintenance des moules, peuvent provoquer des irritations ou des brûlures chimiques par dissolution des tissus cutanés, ont des effets cancérogènes suspectés et ces solvants chlorés provoquent des problèmes respiratoires en cas d’inhalation répétée et ont une toxicité sur le système nerveux central. -
Les risques thermiques des plasturgistes
Toutes les machines de transformation, les étuves et fours de séchage utilisent un apport de calories par chauffage ou frottement ou par le biais d’accélérateurs de chaleur, provoquant des températures de transformation qui s’échelonnent de 100° à 400° environ.
Du fait de ces procédés, les locaux des ateliers de plasturgie sont donc particulièrement exposés aux températures élevées et aux risques de brûlures thermiques.
La proximité d’une source de chaleur peut entrainer des céphalées, hypersudation, tachycardie, hypotension et, conjuguée à des températures de l’air élevée, provoquer des malaises dus à la déshydratation et des troubles circulatoires. Au-delà de 25 oC, l'inconfort se fait ressentir avec, de plus, toutes les conséquences psychologiques que cela peut avoir sur la précision des gestes, la vigilance et donc la sécurité (diminution des capacités de réaction, irritabilité, agressivité).
Les brulures peuvent notamment survenir lors du contact avec les canalisations transportant les fluides caloporteurs pendant les périodes de montage, réglage et maintenance.
Les brulures peuvent aussi être provoquées par des surpressions occasionnant des projections chaudes de matière plastique par les orifices de dégazage, d’alimentation et des buses. -
Les risques physiques des plasturgistes
- Le bruit
Les sources de bruits dans les ateliers de plasturgie sont nombreuses (presses, compresseurs, concasseurs, granulateurs, échappements d’air ou gaz comprimés, soudeuses à ultrasons...), sachant qu’un bruit d’impulsion ayant un caractère soudain et imprévisible est plus nocif qu'un bruit stable et continu. Les niveaux de pression acoustique engendrés par les bruits des machines (sans insonorisation adaptée) dans les ateliers de plasturgie peuvent dépasser 100 dB.
En dehors des atteintes au système auditif (déficit auditif, acouphènes...), le bruit ambiant peut entraîner une gêne ou un stress vecteur de troubles du psychisme et de pathologies qui nuisent non seulement à la santé du travailleur mais aussi à la sécurité de son travail par baisse de vigilance et de dextérité ou de concentration. Des migraines, nausées, vertiges peuvent également survenir suite à l’exposition prolongée et intense aux ultrasons, particulièrement pour les personnes à l’ouïe très fine, notamment chez les jeunes travailleurs, qui peuvent entendre de façon très désagréable les sons très aigus de fréquence supérieure à 16 kHz, alors que la plupart ne les perçoivent pas.
Même sans percevoir vraiment les ultrasons, la pression prolongée exercée dans l’oreille ou transmise par voie osseuse au crane, explique cet effet de malaise, qui survient pour une intensité supérieure à 110 dB généralement pour les personnes sujettes à ces troubles.
- Les vibrations
Les vibrations de machines-outils portatives (ponceuses, meuleuses ...) sont à l’origine d’effets pathologiques sur le membre supérieur (main, coude, épaule), tandis que celles de certaines machines fixes mal calées (presses, concasseurs...) affectent surtout la colonne vertébrale par transmission des vibrations au corps entier. Les expositions des plasturgistes aux vibrations entrainent des troubles ostéoarticulaires (tendinites, lombalgies...), neuropathiques (mal carpien...) et vasculaires.
- Les manutentions
Les charges lourdes portées manuellement, ou le nombre excessif de manipulations et mouvements avec torsion du dos, rotation pour le déplacement, flexion pour le soulèvement (lors des changements de moules par exemple), ou la station debout prolongée ... sont à l’origine d'accidents de travail concernent la colonne vertébrale (dorsalgies, lombosciatiques) et le vieillissement progressif des structures ostéoarticulaires.
- Les incendies et explosions
Les ateliers de plasturgie sont confrontés à un risque potentiel d’inflammation des solvants et d’explosion des poussières de matières plastiques due aux décharges électrostatiques, avec des sources de chaleur nombreuses provoquant de redoutables incendies à la mesure de la quantité de matières plastiques inflammables présentes dans l’atelier, dont la combustion dégage des gaz et fumées très toxiques : oxyde de carbone bien sur, mais aussi acides (chlorhydrique, fluorhydrique, cyanhydrique), anhydride sulfureux, hydrogène sulfuré ... en fonction de la composition des matières plastiques qui peuvent contenir du chlore, du fluor, du soufre ...
Les risques d’incendie-explosion sont présents dans le cas de concentrations de styrène dans l’air atteignant les limites d’explosivité. Le stockage des résines dans des sacs endommagés dans des espaces clos et mal ventilés peut provoquer l’accumulation de vapeurs inflammables (pentane pour l’agent d’expansion du polystyrène).
- Autres risques des plasturgistes
D’autres risques ne sont pas spécifiques au métier de plasturgiste, mais communs à toute activité industrielle : chutes de plain pied sur sol glissant, inégal ou encombré (notamment lors du chargement des trémies d’alimentation), coupures aux mains ou écrasements lors du nettoyage de lame de broyeur par exemple, ou lors des déplacements des éléments mobiles des machines, entraînement par des rotors ou cylindres en rotation, projections de corps étranger dans les yeux, électrisation/électrocution par utilisation d’outillage défectueux ...
Les mesures préventives des risques dans la plasturgie
La prévention la plus efficace est la prévention primaire avec la mise en place de technologies qui permettent des actions sur les produits (suppression ou emploi de produits de substitution de moindre impact potentiel sur l'homme) et/ou des actions sur les procédés (emploi de matériels ou de machines supprimant ou limitant au maximum les impacts, par de très faibles rejets atmosphériques, par de bas niveaux sonores...).
- La suppression / substitution des produits les plus toxiques
Par exemple,
• substituer les colorants à base de chromate de plomb par des pigments organiques,
• choisir une forme physique des adjuvants limitant la production de poussières lors des mélanges,
• utiliser des phtalates non classés ou des plastifiants d'autres familles moins dangereuses.
- L’utilisation de machines et équipements adaptés
→ Machines fermées avec chambre de travail étanche :
Par exemple, la polymérisation du chlorure de vinyle s’effectue en circuit fermé ; néanmoins de petites quantités résiduelles de chlorure de vinyle monomère peuvent se dégager lors du chauffage du PVC et la limite d'exposition est limitée à une concentration moyenne d'exposition de 1 ppm (partie par million en volume d’air) mesurée ou calculée par rapport à une période de référence de 8 heures.
→ Systèmes d'encoffrement et de captage au plus près des émissions, de façon à évacuer les aérosols et les vapeurs :
Il convient de doter les installations de captages localisés et avoir des dispositifs de captage au dessus de l’ensemble des équipements (hottes aspirantes, plafonds filtrants ...), en particulier au niveau des moules lors de l’injection de la matière plastique, afin de maintenir un niveau d’exposition inférieur aux limites réglementaires.
→ Dispositifs de sécurité des machines :
Toute machine doit porter les avertissements, signalisations et dispositifs d’alerte indispensables pour assurer la sécurité des travailleurs afin de supprimer ou réduire au minimum les risques de coupure, d’entraînement, d’écrasement, de cisaillement causés par les éléments exerçant une action directe sur la matière.
Cette identification doit être réalisées par des pictogrammes et couleurs normalisées. Les éléments de travail doivent être disposés, protégés, commandés ou équipés de façon telle que les opérateurs ne puissent atteindre la zone dangereuse. Les panneaux de signalisation seront choisis et disposés de façon à être perçus et compris facilement sans ambiguïté.
Chaque machine doit être munie d’un ou plusieurs dispositifs d’arrêt d’urgence clairement identifiables, accessibles et en nombre suffisant, permettant d’éviter les situations dangereuses en train de se produire :
• Ecrans de protection et de sécurité des opérateurs : protecteurs fixés à l’aide de moyens imposant un outil pour leur démontage ou par des protecteurs mobiles associés à un dispositif de verrouillage.
• Interrupteurs de sécurité.
• Barrières immatérielles de sécurité : des dispositifs électrosensibles de détection de présence et /ou de mouvement verrouillent les mouvements des parties mobiles pendant la présence d’un opérateur.
• Embouts spéciaux antiarrachements
• Capteurs pour mesurer les températures et réguler les dispositifs de chauffage et éviter les surchauffes productrices d’émanations de décomposition thermique dangereuses
• Capteurs pour mesurer les pressions et réguler les dispositifs mécaniques et thermiques et éviter les surpressions internes.
• Ces capteurs sont intégrés dans des systèmes de commande et de contrôle gérés par des automates programmables.
• L’éloignement du personnel des zones dangereuses se fait au moyen d’obstacles fixes tels que panneaux fixes, pleins ou grillagés.
→ Le respect des recommandations des constructeurs et un entretien régulier des machines sont des éléments essentiels pour limiter les risques accidentels et pour prévenir des émanations. Ainsi l’utilisation et l'entretien des machines doivent être effectués par un personnel qualifié, spécifiquement formé (respect scrupuleux des capacités nominale des machines...) : de nombreux cas de fuites accidentelles peuvent survenir au niveau de différents équipements, ce qui entraîne la nécessité d’une maintenance rigoureuse des machines avec contrôle de l'étanchéité.
Des machines utilisées de manière non conforme ou mal entretenues et non vérifiées périodiquement créent un risque chimique supplémentaire. En particulier, les canalisations flexibles doivent être vérifiées périodiquement et remplacées en cas d’usure ou de choc, et en fonction de la durée maximale d’utilisation.
- Une ventilation des lieux de travail adéquate
Les multiples risques chimiques que présentent les matières plastiques ont conduit à de nombreuses réglementations, aboutissant à un ensemble complexe de mesures pour répondre aux normes (valeurs limites d’exposition professionnelle).
La ventilation et l’aération des lieux de travail jouent un rôle essentiel pour limiter la concentration de l'ensemble des toxiques dans l'air ambiant et les évacuer des lieux de travail, de façon à respecter ces valeurs limites et éviter ainsi les conséquences sur la santé des travailleurs. Une ventilation et un appoint d’air appropriés sont aussi indispensables pour empêcher l’accumulation de mélanges inflammables dans l’air. En particulier, une ventilation adéquate des zones de moulage est importante en raison des quantités importantes de vapeur dégagée par les presses de moulage.
Les installations utilisées doivent faire l’objet d’une analyse de risques.
Les analyses et la métrologie des risques sont confiées à des spécialistes de la sécurité au travail (hygiéniste, ingénieur sécurité). Les rapports d’analyses de risques, d’intervention et de maintenance seront intégrés à la documentation de sécurité au travail de l’entreprise (Document Unique de Sécurité).
La ventilation mécanique générale doit assurer un renouvellement d'air en permanence afin de limiter les risques pour la santé, en évitant l’accumulation de vapeurs nocives et explosives, par extraction et soufflage : l'air est transporté dans le local par un ventilateur de soufflage et extrait du local par un ventilateur d'évacuation. L’extraction de l'air se fait grâce à un système de collecte par ces ventilateurs, des gaines de diffusion, et un réseau de conduits qui captent et concentrent les poussières et vapeurs jusqu'aux filtres et aux épurateurs qui permettent de nettoyer l'air, puis de l’évacuer à l'extérieur par rejet dans l'atmosphère.
Les composants aérauliques comme les ventilateurs, les conduits entre autres doivent être accessibles et faciles d’entretien et de nettoyage. En particulier, les réseaux s’encrassent rapidement avec de filtres hors d’usage, une évacuation des condensats obstruée...
- Une installation électrique conforme
L’incendie et/ou l’explosion peuvent provenir des équipements électriques, et en particulier, l’équipotentialité et la bonne mise à la terre de toutes les installations métalliques doivent être contrôlées, les prises défectueuses remplacées, il faut éviter toute accumulation d’électricité
statique ...
Les étincelles, arcs et échauffements provoqués par les moteurs et appareillages électriques en fonctionnement peuvent aussi déclencher la catastrophe.
Il convient d’utiliser de l’appareillage électrique conçu pour atmosphères dangereuses afin de prévenir que le matériel, y compris l’éclairage, soit à l’origine d’un incendie ou d’une explosion.
Une métallisation au moyen d’un matériel conducteur et une mise à la terre appropriées de l'équipement de traitement et de manutention sont utiles pour dissiper et diriger à la terre en toute sécurité les charges électriques accumulées. La protection contre les contacts avec les masses mises accidentellement sous tension est obtenue par un dispositif de coupure automatique en cas de défaut d’isolement.
Il est fortement recommandé de placer des explosimètres dans les zones de réception / manutention / stockage / expédition.
Dans le domaine des atmosphères explosives (Atex), des normes européennes fixent le cadre de travail des industriels et des installateurs. Depuis juin 2003, tout nouveau site de type Atex doit être équipé avec du matériel certifié, avec des enveloppes antidéflagrantes. Les autres installations doivent, depuis juin 2006, avoir été mises à niveau.
- Un stockage des produits rigoureux
Le stockage des monomères et composants auxiliaires présente des risques tels que l’incendie, l’explosion, le risque de chute ou de renversement ou de détérioration d'emballage ... Toutes ces caractéristiques rendent nécessaire, outre les précautions lors de leur emploi, l’aménagement de locaux de stockage, avec des rayonnages métalliques, des planchers et des palettes normalisées. La réduction des risques existants passe par une réflexion sur la structure du local, sur les modalités de rangement et sur les incompatibilités entre les produits. Des procédures de stockage non adaptées peuvent entraîner une fragilisation des emballages à l'origine de fuites ou de ruptures accidentelles, de pollution, de réactions dangereuses ou d'accidents ou induire une modification ou une dégradation des produits qui le rendent plus dangereux car ils peuvent libérer des vapeurs inflammables ou nocives.
L’empilement doit être stable et sa hauteur ne doit pas affecter l’intégrité des emballages.
Le stockage des bidons de solvants, sacs, boites de monomères ou d’adjuvants, doit se faire dans un local ventilé par un système de ventilation mécanique, à l'abri de la chaleur et de l'humidité, et tous les conteneurs de produits chimiques doivent toujours être bien refermés.
L'installation électrique du local de stockage est à réaliser avec du matériel utilisable en atmosphère explosible.
Une bonne tenue des sols des locaux de stockage est essentielle pour éviter l’accumulation des matières déversées.
L’interdiction de fumer dans les locaux doit être absolument respectée et signalée de manière apparente (de même que toutes les autres consignes de sécurité).
Il faut stocker les plus faibles quantités de produits possibles car le risque d'incident ou d'accident croît avec la durée et le volume de stockage.
- La lutte contre le bruit
Les machines et équipements (pompes hydrauliques, broyeurs...), doivent être conçues et fabriquées de façon à ce que les émissions sonores soient réduites au niveau le plus bas possible en application d’une directive européenne 2003/10/CE du 6 février 2003 concernant les prescriptions minimales de sécurité et de santé relatives à l'exposition des travailleurs aux risques dus aux agents physiques liés au bruit.
Par le choix ou l’achat de machines et par l’utilisation de procédés silencieux, les émissions sonores peuvent être maintenues à un bas niveau.
Les machines bruyantes seront, selon les possibilités, munis de capots insonorisants et pour réduire les bruits transmis par les sols et les structures, des blocs anti-vibrations peuvent être placés entre la machine et la surface d’appui.
Les échappements d’air comprimé des circuits pneumatiques sont à équiper d’un silencieux. Les postes de commande et de contrôle peuvent se situer dans un local séparé avec une isolation phonique.
Quant aux ultrasons, la pose d’une simple enceinte acoustique supplémentaire (capotage) suffit généralement à protéger totalement le poste de travail.
En ce qui concerne les locaux, les réflexions sur les murs entraînent une augmentation du niveau sonore dans le local et des mesures préventives de correction acoustique comme la mise en place d’un plafond absorbant, de cloisons amovibles à proximité des installations, réduisent à la fois le niveau sonore et protègent les postes de travail avoisinants.
- Une bonne hygiène
Une bonne tenue des locaux est essentielle pour éviter l’accumulation de déversements et de poussières sous ou autour des machines de moulage. Les déversements peuvent créer un danger de glissement et par conséquent doivent être nettoyés immédiatement. De même, il convient de ramasser et enlever la poussière créée par les opérations de découpage et de broyage etc.
Des postes de rinçage oculaire et les douches de sécurité doivent se trouver à proximité des postes de travail.
- Des aides à la manutention
Les nombreuses manutentions manuelles de charges lourdes qui entraînent des risques évidents de troubles musculo-squelettiques au niveau du dos et des articulations, peuvent être réduits par l’utilisation systématique de manutention assistée et de moyens de mise à niveau et de préhension des charges, en particulier des moules : ponts roulants, chariots, moyens de levage appropriés...
- Le port d’équipements de protection individuel adéquat
Les équipements de protection individuelle sont nécessaires pour réduire le risque d’exposition non totalement éliminé par les mesures de protection collectives précédentes : masques respiratoires filtrants, gants, vêtements de protection, chaussures et lunettes de sécurité.
En cas d’urgence ou pour des travaux exceptionnels d’entretien de courte durée, si le système de ventilation ne suffit pas à empêcher l’accumulation de vapeurs ou de poussières, un appareil de protection respiratoire adéquat doit être fourni : masque à cartouche avec un filtre adapté au produit.
S’il y a possibilité de contact avec la main lors des transvasements par exemple, il s’avère indispensable de porter des gants de protection adaptés à la tâche effectuée et au produit manipulé : il n'existe pas de gant de protection universel. Le type de gants conseillé, imperméables, à longues manchettes, pour éviter la pénétration des produits à l’intérieur, doit être adapté aux différents produits manipulés selon leur composition qui figure sur la Fiche de Sécurité (FDS).
Il est recommandé de porter des vêtements à manches longues et des combinaisons aux propriétés antistatiques et ininflammables, surtout lors des interventions près des surfaces chaudes (moules chauffés...) et sur les circuits de fluides caloporteurs
- La formation et l’information du personnel
La formation, par un organisme agréé, sur les dangers des produits utilisés et sur les moyens de se protéger, est indispensable : par exemple, comprendre les étiquettes du contenant des produits, connaître l’attitude à adopter en cas de fuite ou de déversement accidentel, savoir utiliser les E.P.I adéquats, formation aux premiers secours et incendie...
Pour aller plus loin
Dossier INRS ED 638 : Matières plastiques et adjuvants. Hygiène et sécurité (226 pages, 2006)
Septembre 2011
Partagez et diffusez ce dossier
Laissez un commentaire
Votre adresse de messagerie ne sera pas publiée.