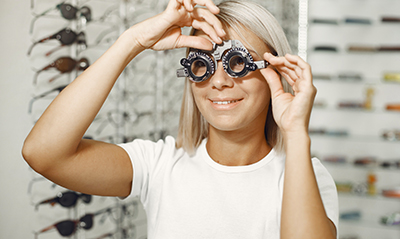
L'industrie textile transforme les fibres naturelles et synthétiques en tissu pour la fabrication de produit semi-finis (fils, étoffes...) ou entièrement ouvrés tels les vêtements, le linge ... Ces opérations s'effectuent à l'aide de machines bruyantes et dangereuses à cause de pièces en mouvement susceptibles d'entrainer des blessures des membres supérieurs. Par ailleurs, au cours de la transformation, les matières fibreuses subissent différentes opérations d'ennoblissement qui utilisent beaucoup de substances chimiques, dont certaines sont allergènes, d'autres cancérogènes. La fabrication textile génère aussi une quantité considérable de poussières, responsables de maladies pulmonaires et plusieurs métiers du textile exposent les travailleurs à la chaleur humide. Enfin, les risques de Troubles Musculo Squelettiques (TMS) sont très présents dans l'industrie textile.
L'industrie textile transforme les fibres naturelles (coton, lin, laine,...) et synthétiques en tissu pour la fabrication de produit semi-finis (fils, étoffes...) ou entièrement ouvrés tels les vêtements, le linge ...
Ces opérations de cardage, filage, ourdissage, tissage, tricotage, s'effectuent à l'aide de machines bruyantes et dangereuses à cause de pièces en mouvement susceptibles d'entrainer des coupures, des lacérations, des écrasements des membres supérieurs. Par ailleurs, au cours de la transformation, les matières fibreuses subissent différentes opérations d'ennoblissement (blanchissement, teinture avec des colorants, impression, apprêts) qui utilise beaucoup de substances chimiques, dont certaines sont allergènes, d'autres cancérogènes. La fabrication textile génère aussi une quantité considérable de poussières, fibres en suspension dans l'air des ateliers, responsables de maladies pulmonaires et plusieurs métiers du textile exposent les travailleurs à la chaleur humide. Enfin, les risques de Troubles Musculo Squelettiques (TMS) liés aux manutentions de lourds objets (bobines de fils, cartons...) sont très présents dans l'industrie textile.
Par des mesures de prévention appropriées, collectives et individuelles, on peut réduire toutes ces expositions et diminuer fortement les risques professionnels dans les industries textiles.
Les principaux risques dans les industries textiles
- LES RISQUES PHYSIQUES
- Risques liés aux machines
Certaines parties des machines (transmissions, points de pincements, peignes...), les opérations de nettoyage et de maintenance, les réglages, les démarrages sont sources d'accidents majeurs du fait des pièces en mouvement en particulier lors des mises en marche intempestives, des arrêts anormaux suite à un bourrage ou à une rupture d'énergie : piqures, coupures aux mains, lacérations des avant-bras ou écrasements lors des nettoyages par exemple, ou lors des déplacements des éléments mobiles des machines, entraînement, happement, friction, enroulement des cheveux et des vêtements par des rouleaux ou cylindres en rotation, retour de projectile (pièces de carde, outils, poussières) ...
Par ailleurs, de nombreux troubles musculo-squelettiques sont dus aux vibrations et aux mouvements répétés chez des travailleurs exerçant sur des machines qui fonctionnent à vitesse élevée. Enfin, le déconditionnement des balles (feuillards) peuvent occasionner des coupures aux mains.
- Le bruit
Les sources de bruits dans les ateliers de textile sont nombreuses, créant un environnement bruyant du fait de toutes les machines en fonctionnement. Les niveaux de pression acoustique engendrés par les bruits des machines (sans insonorisation adaptée) dans ces ateliers peuvent dépasser 90 dB.
En dehors des atteintes au système auditif (déficit auditif, acouphènes...), le bruit ambiant peut entraîner une gêne ou un stress vecteur de troubles du psychisme et de pathologies qui nuisent non seulement à la santé du travailleur mais aussi à la sécurité de son travail par baisse de vigilance et de dextérité ou de concentration.
- Les manutentions
De nombreuses charges lourdes sont portées manuellement, et/ou il y a un nombre excessif de manipulations et mouvements avec torsion du dos, rotation pour le déplacement, flexion pour le soulèvement : dépose de lourds cylindres, d'ensouples pour alimenter le métier à tisser, port de multiples bobines de fils et leurs cartons, postures contraignantes pour charger ou décharger les cantres pour dérouler les bobines, ou pour tirer la matière en cas de bourrage. Tous ces éléments, y compris une station debout prolongée, sont à l'origine d'accidents de travail concernent la colonne vertébrale (dorsalgies, lombosciatiques) et le vieillissement progressif des structures ostéoarticulaires des membres supérieurs (tendinites de l'épaule, épicondylite du coude, syndrome du canal carpien au poignet).
- Les risques thermiques
Du fait de certains procédés, les locaux des ateliers textiles sont exposés à l'humidité et aux températures élevées qui peuvent entrainer des céphalées, hypersudation, tachycardie, hypotension, crampes musculaires, troubles circulatoires et provoquer des malaises dus à la déshydratation. Au-delà de 25 oC, l'inconfort se fait ressentir avec, de plus, toutes les conséquences psychologiques que cela peut avoir sur la précision des gestes, la vigilance et donc la sécurité (diminution des capacités de réaction, irritabilité, agressivité).
- Autres risques
D'autres risques ne sont pas spécifiques au métier du textile, mais communs à toute activité industrielle : chutes de plain pied sur sol glissant ((huile, graisse, eau), inégal ou encombré (notamment de pièces de machine), projections de corps étranger dans les yeux, électrisation/électrocution par présence de circuits défectueux ou mal protégés, incendie avec des fibres combustibles au contact ou à proximité des points chauds (moteurs, roulements, courroies...) , notamment en cas de surchauffe, ou explosion de poussière dans un lieu confiné ... - LES RISQUES CHIMIQUES
La composition chimique des fibres textiles varie d'une famille à l'autre en fonction des matériaux utilisés et des produits chimiques ajoutés dans les opérations de prétraitement (lavage, blanchiment, mercerisation pour donner un aspect lustré), de teinture pour coloration ou dans l'ajout d'adjuvants pour leur conférer des propriétés biocides (contre les puces, mites, moustiques, acariens...) : ces substances sont pour certaines toxiques, allergisantes voire cancérogènes à plus ou moins long terme.
- Risques des fibres textiles
Les fibres textiles sont soit des fibres naturelles végétales (coton, lin, ...) ou animales (laine, soie...) soit des fibres chimiques artificielles, élaborées à partir de la cellulose (acétate, triacétate de cellulose, viscose, fibres polynosiques ...) ou synthétiques, élaborées à partir d'hydrocarbures par la pétrochimie (fibres polyacryliques, polyamides, polyesters, polyvinyliques...).
Ces substances filamenteuses sont caractérisées par leur finesse et leur forme très allongée par rapport à leur épaisseur : la plupart de ces fibres mesurent entre 10 et 150 millimètres de long pour une épaisseur de 10 à 50 microns.
En ce qui concerne les risques professionnels, les fibres textiles sont plus épaisses que les fibres d'amiante, de verre ou de céramique qui ont des diamètres inférieurs à 5 µm, et elles pénètrent moins profondément dans le poumon et y séjournent moins : de ce point de vue, elles sont donc moins dangereuses, mais l'inhalation excessive de poussières textiles est néanmoins la cause de certaines maladies pulmonaires comme la bronchite chronique, la maladie pulmonaire obstructive chronique (MPOC), l'asthme et la byssinose, resserrement transitoire des voies respiratoires s'apparentant à l'asthme et donnant la « fièvre de filature » ou « fièvre du lundi ». Les allergènes divers (micro-organismes bactériens et fongiques avec leurs toxines, acariens, pesticides) sont en partie responsables de ces affections respiratoires, avec une susceptibilité individuelle variable et le tabagisme comme cofacteur aggravant majeur.
Les opérations préliminaires, ouverture des balles, cardage ou peignage, étirage, sont les opérations les plus exposantes aux poussières de fibres textiles. Il existe un risque accru de cancer colorectal chez les travailleurs de l'industrie du textile, surtout en ce qui concerne les travailleurs exposés aux fibres de polypropylène dans les ateliers d'extrusion.
- Risques des colorants et apprêts
Les colorants utilisés dans les ateliers de teintures sont responsables d'eczéma, urticaire, et d'asthme. Les colorants contenant de l'auramine, des amines aromatiques... sont des substances possiblement cancérogènes, et même certainement pour quelques-uns de ces composés (benzidine, beta-naphtylamine...).
Le diméthylformamide, utilisé comme solvant pour le traitement de tissus est un toxique hépatique.
Le formaldéhyde utilisé dans l'impression, l'apprêtage provoque des irritations de la peau, des yeux, des allergies cutanées et respiratoires, et est susceptible d'entrainer un cancer du nasopharynx.
La fabrication de textiles est classé comme activité cancérogène par le CIRC (Centre International de Recherche contre le Cancer) compte tenu des résultats d'études épidémiologiques, sans qu'il soit possible d'en attribuer la responsabilité à une substance particulière.
Les mesures préventives des risques dans les industries textiles
La prévention la plus efficace est la prévention primaire avec la mise en place de technologies qui permettent des actions sur les produits (suppression ou emploi de produits de substitution de moindre impact potentiel sur l'homme) et/ou des actions sur les procédés (emploi de matériels ou de machines supprimant ou limitant au maximum les impacts, par de très faibles rejets atmosphériques, par de bas niveaux sonores...).
La prévention collective implique l'utilisation de systèmes de fabrication isolés et automatisés et de dispositifs mécaniques comme l'extraction de poussières et de vapeurs qui permettent de réduire l'exposition des travailleurs, en particulier lorsque l'on ne peut pas remplacer des produits chimiques dangereux par d'autres pour des raisons techniques.
Enfin, le port d'équipement de protection individuel (combinaison, gants, chaussures et lunettes de protection, masques...) est obligatoire pour réduire le risque d'exposition non totalement éliminé par les mesures de protection collectives, ainsi que la présence d'installations et de matériel de premier secours.
- L'identification, la suppression / substitution des produits les plus toxiques
La première étape consiste à repérer en particulier les agents chimiques cancérogènes ou dangereux dans le cadre de l'évaluation des risques du Document Unique de Sécurité (DUS).
Les Fiches de Données de Sécurité (FDS), obligatoires pour tout produit chimique dangereux, comportent les renseignements relatifs à la toxicité des produits, donc notamment leur caractère cancérogène éventuel. - L'utilisation de machines et équipements adaptés
Toute machine doit porter les avertissements, signalisations et dispositifs d'alerte indispensables pour assurer la sécurité des travailleurs afin de supprimer ou réduire au minimum les risques de coupure, d'entraînement, d'écrasement, de cisaillement causés par les éléments exerçant une action directe sur la matière.
Cette identification doit être réalisées par des pictogrammes et couleurs normalisées. Les éléments de travail doivent être disposés, protégés, commandés ou équipés de façon telle que les opérateurs ne puissent atteindre la zone dangereuse.
Les panneaux de signalisation seront choisis et disposés de façon à être perçus et compris facilement sans ambiguïté.
Chaque machine doit être munie d'un ou plusieurs dispositifs d'arrêt d'urgence clairement identifiables, accessibles et en nombre suffisant, permettant d'éviter les situations dangereuses en train de se produire :
- Ecrans de protection et de sécurité des opérateurs : protecteurs (carter, couvercle, écran, porte, ...) fixés à l'aide de moyens imposant un outil pour leur démontage ou par des protecteurs mobiles (enceintes...) associés à un dispositif de verrouillage. Par exemple protections fixes contre le pincement près du point d'entraînement.
- Interrupteurs de sécurité.
- Barrières immatérielles de sécurité : des dispositifs électro-sensibles de détection de présence et /ou de mouvement verrouillent les mouvements des parties mobiles pendant la présence d'un opérateur, comme des barres sensibles ou des protections à capteurs photoélectriques.
La vérification de la mise en place, du bon état de la fonctionnement des protecteurs, des dispositifs de verrouillage ou d'inter-verrouillage et dispositifs de protection (arrêt d'urgence...) est fondamentale, pour assurer par exemple les consignes d'arrêt obligatoire des cylindres, notamment lors des incidents et des opérations de maintenance , pour lesquelles une véritable procédure de consignation et déconsignation doit être mise en œuvre.
Le respect des recommandations des constructeurs et un entretien régulier des machines sont des éléments essentiels pour limiter les risques accidentels. Ainsi l'utilisation et l'entretien des machines doivent être effectués par un personnel qualifié, spécifiquement formé : des machines utilisées de manière non conforme ou mal entretenues et non vérifiées périodiquement créent un risque supplémentaire. - La lutte contre le bruit
Les machines et équipements doivent être conçus et fabriqués de façon à ce que les émissions sonores soient réduites au niveau le plus bas possible en application d'une directive européenne 2003/10/CE du 6 février 2003 concernant les prescriptions minimales de sécurité et de santé relatives à l'exposition des travailleurs aux risques dus aux agents physiques liés au bruit.
Par le choix ou l'achat de machines et par l'utilisation de procédés silencieux, les émissions sonores peuvent être maintenues à un bas niveau.
Les machines bruyantes seront, selon les possibilités, munis de capots insonorisants et pour réduire les bruits transmis par les sols et les structures, des blocs anti-vibrations peuvent être placés entre la machine et la surface d'appui. Les fixations doivent être maintenues en bon état, les bruits parasites dus aux roulements... doivent être éliminés par un dépoussiérage et graissage réguliers.
Les postes de commande et de contrôle peuvent se situer dans un local séparé avec une isolation phonique.
En ce qui concerne les locaux, les réflexions sur les murs entraînent une augmentation du niveau sonore dans le local et des mesures préventives de correction acoustique comme la mise en place d'un plafond ou faux-plafond absorbant, de cloisons amovibles recouvertes de produit anti-réverbérant à proximité des installations, réduisent à la fois le niveau sonore et protègent les postes de travail avoisinants. - Une ventilation des lieux de travail adéquate
Les multiples risques chimiques que présentent les industries textiles ont conduit à de nombreuses réglementations, aboutissant à un ensemble complexe de mesures pour répondre aux normes (valeurs limites d'exposition professionnelle).
La ventilation et l'aération des lieux de travail jouent un rôle essentiel pour limiter la concentration de l'ensemble des toxiques dans l'air ambiant et les évacuer des lieux de travail, de façon à respecter ces valeurs limites et éviter ainsi les conséquences sur la santé des travailleurs. Une ventilation et un appoint d'air appropriés sont aussi indispensables pour empêcher l'accumulation de mélanges inflammables dans l'air.
Les installations utilisées doivent faire l'objet d'une analyse de risques.
Les analyses et la métrologie des risques sont confiées à des spécialistes de la sécurité au travail (hygiéniste, ingénieur sécurité). Les rapports d'analyses de risques, d'intervention et de maintenance seront intégrés à la documentation de sécurité au travail de l'entreprise (Document Unique de Sécurité). La surveillance de la concentration de poussières dans l'air doit être entreprise régulièrement afin de vérifier l'efficacité des mesures préventives dans la réduction de l'exposition.
La ventilation mécanique générale doit assurer un renouvellement d'air en permanence afin de limiter les risques pour la santé, en évitant l'accumulation de vapeurs nocives et explosives, par extraction et soufflage : l'air est transporté dans le local par un ventilateur de soufflage et extrait du local par un ventilateur d'évacuation. L'extraction de l'air se fait grâce à un système de collecte par ces ventilateurs, des gaines de diffusion, et un réseau de conduits qui captent et concentrent les poussières et vapeurs jusqu'aux filtres et aux épurateurs qui permettent de nettoyer l'air, puis de l'évacuer à l'extérieur par rejet dans l'atmosphère.
Les composants aérauliques comme les ventilateurs, les conduits entre autres doivent être accessibles et faciles d'entretien et de nettoyage. En particulier, les réseaux s'encrassent rapidement avec des filtres hors d'usage, une évacuation des condensats obstruée...
Réduire la concentration de poussières dans l'environnement passe aussi en procédant au nettoyage fréquent par aspiration mécanique centralisée (pour remplacer soufflette et balai qui dispersent à nouveau les particules dans l'air) et, si possible, par la suppression localisée de la poussière par captation à la source. - Une installation électrique conforme
L'incendie et/ou l'explosion peuvent provenir des équipements électriques, et en particulier, l'équipotentialité et la bonne mise à la terre de toutes les installations métalliques doivent être contrôlées, les prises défectueuses remplacées, il faut éviter toute accumulation d'électricité statique. Les étincelles, arcs et échauffements provoqués par les moteurs et appareillages électriques en fonctionnement peuvent aussi déclencher la catastrophe.
Il convient d'utiliser de l'appareillage électrique conçu pour atmosphères dangereuses afin de prévenir que le matériel, y compris l'éclairage, soit à l'origine d'un incendie ou d'une explosion.
Une métallisation au moyen d'un matériel conducteur et une mise à la terre appropriées de l'équipement de traitement et de manutention sont utiles pour dissiper et diriger à la terre en toute sécurité les charges électriques accumulées. La protection contre les contacts avec les masses mises accidentellement sous tension est obtenue par un dispositif de coupure automatique en cas de défaut d'isolement.
Il est fortement recommandé de placer des explosimètres dans les zones de réception / manutention / stockage / expédition.
Dans le domaine des atmosphères explosives (Atex), des normes européennes fixent le cadre de travail des industriels et des installateurs. Depuis juin 2003, tout nouveau site de type Atex doit être équipé avec du matériel certifié, avec des enveloppes antidéflagrantes. Les autres installations doivent, depuis juin 2006, avoir été mises à niveau. - Un stockage des produits rigoureux
Le stockage des produits chimiques présente des risques tels que l'incendie, l'explosion, le risque de chute ou de renversement ou de détérioration d'emballage ... Toutes ces caractéristiques rendent nécessaire, outre les précautions lors de leur emploi, l'aménagement de locaux de stockage, avec des rayonnages métalliques, des planchers et des palettes normalisées. La réduction des risques existants passe par une réflexion sur la structure du local, sur les modalités de rangement et sur les incompatibilités entre les produits. Des procédures de stockage non adaptées peuvent entraîner une fragilisation des emballages à l'origine de fuites ou de ruptures accidentelles, de pollution, de réactions dangereuses ou d'accidents ou induire une modification ou une dégradation des produits qui le rendent plus dangereux car ils peuvent libérer des vapeurs inflammables ou nocives.
L'empilement doit être stable et sa hauteur ne doit pas affecter l'intégrité des emballages.
Le stockage doit se faire dans un local ventilé par un système de ventilation mécanique, à l'abri de la chaleur et de l'humidité, et tous les conteneurs de produits chimiques doivent toujours être bien refermés.
L'installation électrique du local de stockage est à réaliser avec du matériel utilisable en atmosphère explosible.
Une bonne tenue des sols des locaux de stockage est essentielle pour éviter l'accumulation des matières déversées.
L'interdiction de fumer dans les locaux doit être absolument respectée et signalée de manière apparente (de même que toutes les autres consignes de sécurité).
Il faut stocker les plus faibles quantités de produits possibles car le risque d'incident ou d'accident croît avec la durée et le volume de stockage. - Une bonne tenue des locaux
Une bonne tenue des locaux est essentielle pour éviter l'accumulation de déversements et de poussières sous ou autour des machines. Les déversements peuvent créer un danger de glissement et par conséquent doivent être nettoyés et immédiatement épongé avec des absorbants.
La circulation et l'état des sols sont à l'origine de nombreux accidents ; à ce titre, le balisage, l'éclairage et la sécurisation des voies de circulation et des zones de stockage sont essentielles ainsi que le rangement en permanence et l'entretien des sols assurent la prévention des risques de chutes et de heurts.
- Pour la prévention des risques de chute de plain-pied, des revêtements de sol antidérapants doivent être privilégiés, les inégalités de surfaces et/ou obstacles doivent être soit supprimés (bouchage des trous) soit clairement signalés, notamment dans les lieux de passage.
- Il faut veiller à maintenir l'atelier rangé. Les voies de circulation doivent être débarrassées de tout obstacle. Il faut éviter les zones d'ombre en optimisant l'éclairage et signaler les escaliers, les dénivelés, les encombrements temporaires, et prévoir des aires de rangement pour les organes démontés, les pièces en attente de remontage.
- Les allées de circulation (piétons/véhicules) doivent être nettement délimitées et de largeur suffisante. Les endroits pouvant présenter un risque de danger (croisements, rétrécissements...) doivent être très nettement signalés. - Des aides à la manutention
Les nombreuses manutentions manuelles de charges lourdes qui entraînent des risques évidents de troubles musculo-squelettiques au niveau du dos et des articulations, peuvent être réduits par l'utilisation systématique de manutention assistée et de moyens de mise à niveau et de préhension des charges, en particulier des rouleaux, grilles, bobines : ponts roulants, chariots, moyens de levage appropriés tels des bras hydrauliques articulés, moyens de préhension avec poignées ergonomiques, soutien des carters par vérin, par béquille, crochets pour débourrage... - Le port d'équipements de protection individuel adéquat
Les équipements de protection individuelle sont nécessaires pour réduire le risque d'exposition non totalement éliminé par les mesures de protection collectives précédentes : gants, vêtements de protection, chaussures et lunettes de sécurité.
S'il y a possibilité de contact avec la main lors des transvasements par exemple, il s'avère indispensable de porter des gants de protection adaptés à la tâche effectuée et au produit manipulé : il n'existe pas de gant de protection universel.
Le type de gants conseillé, imperméables, à longues manchettes, pour éviter la pénétration des produits à l'intérieur, doit être adapté aux différents produits manipulés selon leur composition qui figure sur la Fiche de Sécurité (FDS). Des gants appropriés doivent être aussi utilisés pour le conditionnement ou le déconditionnement (feuillards, fil de fer) pour éviter les coupures aux mains.
En cas d'urgence ou pour des travaux exceptionnels d'entretien de courte durée, si le système de ventilation ne suffit pas à empêcher l'accumulation de vapeurs ou de poussières, un appareil de protection respiratoire adéquat doit être fourni pour éviter l'exposition à une concentration élevée : masque à cartouche avec un filtre adapté au produit.
Des postes de rinçage oculaire et les douches de sécurité doivent se trouver à proximité des postes de travail pour ôter les projections de poussières ou autres corps étrangers dans les yeux. - La surveillance médicale
Pour les travailleurs exposés à la poussière, il faut réaliser des visites médicales régulières :
- Tests respiratoires (spiromètre) à l'embauche pour détecter une déficience des fonctions pulmonaires et tous les 2 ans pour dépister l'apparition des troubles respiratoires.
- Radiographie thoracique si nécessaire. - La formation et l'information du personnel
La formation, par un organisme agréé, sur les dangers des produits utilisés et sur les moyens de se protéger, est indispensable : par exemple, comprendre les étiquettes du contenant des produits, informer sur le risque potentiel de maladies pulmonaires et sur les moyens de les prévenir, connaître l'attitude à adopter en cas de fuite ou de déversement accidentel, savoir utiliser les E.P.I adéquats, formation aux premiers secours et incendie...
Avril 2012
Partagez et diffusez ce dossier
Laissez un commentaire
Votre adresse de messagerie ne sera pas publiée.