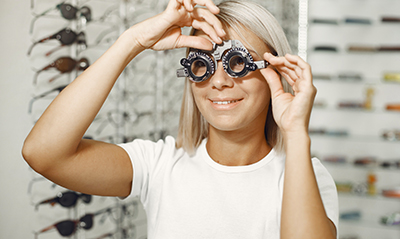
- Accueil
- Formation Conseils
- Fiches Métier
- La prévention des risques professionnels dans les fonderies
Les opérateurs de fonderie élaborent, des pièces volumineuses en alliages pour des fabrications unitaires ou en séries, artisanales ou mécanisées. De nombreux agents chimiques dangereux sont utilisés : les affections respiratoires sont des maladies professionnelles préoccupantes pour les fondeurs, avec la possibilité d’apparition de cancers. Par ailleurs, la nature même des procédés de fonderie à partir de métal en fusion exposent évidemment à un risque de brûlure thermique par projection de métal ou exposition aux rayons infrarouges...
Les opérateurs de fonderie élaborent, à partir de métaux, des pièces volumineuses ou non, en alliages ferreux ou d’étain, bronze, laiton ou autres métaux non ferreux (cuivre, plomb, aluminium...) par coulée dans des moules, pour des fabrications unitaires ou en séries, artisanales ou mécanisées.
De nombreux agents chimiques dangereux (silice cristalline, formaldéhyde, Hydrocarbures Aromatiques Polycycliques, fumées des alliages métalliques liquides, Fibres Céramiques Réfractaires...) sont utilisés ou émis lors des différents procédés de moulage en sable et noyaux qui utilisent également des résines dont la dégradation thermique pendant la coulée génèrent des substances toxiques : les affections respiratoires sont des maladies professionnelles préoccupantes pour les fondeurs, avec la possibilité d’apparition de cancers.
Par ailleurs, la nature même des procédés de fonderie à partir de métal en fusion exposent évidemment à un risque de brûlure thermique par projection de métal ou exposition aux rayons infrarouges. Les accidents du travail provoqués par des blessures aux mains ou des corps étrangers dans les yeux sont également très fréquents.
De plus, il faut prendre en compte les risques professionnels non spécifiques à la fonderie, liés aux manutentions, aux chutes de plain-pied, à la possibilité des contacts avec des conducteurs électriques sous tension, aux troubles auditifs liés à des niveaux sonores élevés...
Par des mesures de prévention appropriées, on peut réduire toutes ces expositions et diminuer fortement les risques professionnels dans les fonderies.
Les principaux risques dans les fonderies
Les fondeurs peuvent exercer leurs activités dans des fonderies intégrées ou non mettant en œuvre différents types de matériaux :
- alliages ferreux (fontes, aciers...),
- alliages légers (aluminium, magnésium),
- alliages cuivreux (bronze, laiton),
- alliages lourds (plomb, zamak).
Ces fonderies utilisent différents procédés pour produire des pièces de petites ou de grandes dimensions :
- moulage main ou mécanisé,
- moulage en moule métallique, coulée gravitaire ou sous pression,
- obtention de pièces mécaniques par moulage en cire perdue,
- moulage d’art.
La mise en œuvre de la production (préparation des outillages et des matériaux, moules, noyaux, élaboration d’alliages, fusion de l’alliage, coulée, parachèvement par meulage et ébarbage, ...) concernent différents postes de travail. Le moulage manuel unitaire ou petite série, le moulage mécanisé avec systèmes automatisés pour grande série, le moulage d’art à cire perdue sont différents procédés qui ont néanmoins en commun plusieurs caractéristiques : conduire un four de fusion, amener l’alliage aux conditions de coulée (état, température...), réaliser des noyaux à prise chimique en sable, en céramique, en cire ou en résine thermodurcissable, procéder à la coulée, décocher, parachever...Dans toutes ces activités, les travaux de fonderie utilisent des fours pour obtenir l’alliage en fusion qui exposent à de fortes chaleurs et aux rayons infrarouges et utilisent de nombreux produits chimiques, dont certains sont allergènes et cancérogènes. Les risques thermiques liés au métal liquide, chimiques liés aux produits utilisés et physiques liés aux manutentions, aux machines... font de la fonderie une activité très accidentogène.
- Les risques thermiques causés par les procédés de fonderie
Lors de la production de métal en fusion, la température du four (électrique, à gaz...) est de l’ordre de 1000°C pour de nombreux alliages, mais le couvercle des poches, du chenal de coulée peut atteindre 1200°C, les louches 1500 °C ; la chaleur des fours pour certains alliages est moins forte (par exemple 300 à 500°C pour l’étain), mais toujours très élevée.
Du fait de ces procédés, les locaux des ateliers de fonderie sont donc particulièrement exposés à l’énergie rayonnante des infrarouges, aux températures élevées et aux risques de brûlures thermiques. Le suivi de la fusion, la proximité du métal en fusion, le contact avec des machines ou outillages chauds, le décrassage de la surface du bain liquide, de la poche de coulée, et notamment pendant les périodes de montage, réglage et maintenance sont les principales sources de risque thermique.
Le contact direct de la peau avec des surfaces chaudes ou des métaux en fusion peut bien entendu d’abord provoquer de très graves brûlures cutanées, lors du transport du métal fondu ou par flammèches et coulures lors du décrassage.
Mais la proximité d’une source de chaleur peut aussi entrainer des céphalées, hypersudation, tachycardie, hypotension et, conjuguée à des températures de l’air élevée, provoquer des malaises dus à la déshydratation et des troubles circulatoires. Au-delà de 25 oC, l'inconfort se fait ressentir avec, de plus, toutes les conséquences psychologiques que cela peut avoir sur la précision des gestes, la vigilance et donc la sécurité (diminution des capacités de réaction, irritabilité, agressivité).
Les expositions au rayonnement infrarouge provenant du métal en fusion, dont la densité de puissance transférable est beaucoup plus forte qu’en convection, peuvent augmenter le risque de cataracte et d’altération rétinienne et cornéenne ou de brûlures ou d’irritations cutanées. Les risques oculaires sont fortement aggravés par les rayons directs lorsque le travailleurfixe la source IR de manière prolongée, en restant immobile dans son axe, mais il faut aussi tenir compte des rayons indirects par réflexion sur des surfaces réfléchissantes. - Les risques chimiques causés par les procédés de fonderie
Les fumées émises par les alliages métalliques liquides
Toutes les fumées de métaux peuvent entrainer des pathologies respiratoires (toux, expectoration, essoufflement), particulièrement pour certains alliages avec des oxydes de métaux dangereux pour la santé (plomb, nickel, chrome...) qui peuvent également être présents dans les fumées.
L’intoxication chronique au plomb, par inhalation de fumées et de poussières, expose les travailleurs à des maladies professionnelles à long terme (saturnisme), par effets cumulatifs : troubles du système nerveux, anémie, insuffisance rénale, altération de la fertilité.
Des cancers (ethmoïde, sinus, bronches) peuvent être causés par le dioxyde de nickel.
La fièvre des fondeurs, avec des symptômes de type grippal, provient d’une forte inhalation d’oxyde de zinc, mais également de fumées à base de cuivre, magnésium ou cadmium.
Les fumées d’oxydes métalliques sont par ailleurs allergisantes et peuvent être à l’origine de véritables asthmes professionnels, urticaire, œdème de Quincke.
Les poussières de silice cristalline
Le sable de fonderie utilisé pour la fabrication des moules, sous forme de poussières riches en silice cristalline peut provoquer une silicose et est classée comme cancérogène avérée par le CIRC : l’exposition a lieu à la sablerie lors du mélange et du transport, lors du noyautage et du moulage, lors du décochage (séparation du sable des pièces), et un peu lors du parachèvement des pièces (ébarbage, meulage des pièces).
Les particules de poussières de silice cristalline peuvent être très fines (d’un diamètre inférieur à 5 microns) et sont donc invisibles à l’œil nu, et restent longtemps en suspension dans l’air ambiant.
En étant inhalées et en séjournant longtemps dans le tissu pulmonaire, les très fines poussières de silice provoquent une inflammation chronique des muqueuses pulmonaires, la formation d'un tissu pulmonaire fibreux, la constitution de nodules, entrainant une maladie respiratoire, une pneumoconiose fibrosante nommée silicose, se traduisant par un essoufflement à l’effort (dyspnée) et de la toux au début, jusqu’à une déficience respiratoire très grave et une insuffisance cardiaque (tableau n°25 des maladies professionnelles du Régime Général). La silicose affecte la fonction pulmonaire au point de favoriser le développement de cancers broncho-pulmonaires : la silice est classée comme cancérogène avéré par le CIRC mais n’est classée par l’Union européenne que comme Agent Chimique Dangereux (ACD).
Par ailleurs, les poussières de silice cristalline peuvent induire une irritation des yeux et provoquer l’apparition de bronchites chroniques.
Les résines et les produits de dégradation thermique pendant la coulée
Le secteur du moulage et la réalisation des noyaux à prise chimique avec des résines thermodurcissables génèrent des émissions de formaldéhyde, de phénol, et les catalyseurs de polymérisation, du diméthyléthylamine (DMEA), du formiate de méthyle selon le type de procédé. L’alcool furfurylique et le diisocyanate de diphénylméthane (MDI) peuvent être aussi émis lors de la mise en œuvre des résines.
Ces produits sont irritants pour la peau et les muqueuses, les yeux, les voies respiratoires.
Le formaldéhyde est classé comme cancérogène.
Les hydrocarbures aromatiques polycycliques (HAP) sont formés lors de la pyrolyse de produits organiques (liants des moules en sable, graisses utilisées lors du moulage sous pression et en coquille,...) et certains d’entre eux sont également classés comme cancérogènes.
Enfin, du monoxyde de carbone (CO), qui se forme lors de la combustion des liants organiques des moules, peut provoquer une grave asphyxie.
Les fibres céramiques réfractaires (FCR)
Les FCR sont utilisées en fonderie comme isolant thermique pour le garnissage des fours, l’isolation des conduites, des couvercles et plaques de protection, des outils...
Les poussières de fibres céramiques réfractaires FCR, ont un risque cancérogène moindre que l’amiante, mais sont néanmoins classées en catégorie 2 (phrase de risque R 49, c'est-à-dire possibilité pour ces produits d’être cancérigène pour l’homme).
De plus, sous l’action de la chaleur, les FCR peuvent se transformer partiellement en produits pulvérulents contenant de la silice cristalline, ce qui entraine un risque potentiel de silicose.
Par ailleurs, l’inhalation constante dans les poumons de FCR peut causer des rhinites allergiques ou des inflammations de la muqueuse nasale, des pneumopathies chroniques et de l’asthme.
Le risque est le plus important lors du renouvellement des FCR, soit de manière préventive lors de maintenance régulière sur les fours, soit de manière curative lors d’un constat d’usure. - Les risques physiques dans les fonderies
Risques liés aux machines et outillages
Les machines à mouler, à noyauter, à injecter les cires et leurs périphériques (systèmes de déboitage, ébavurage...) sont susceptibles d’avoir des organes en mouvement qui provoquent des risques de coupure aux mains, de lacérations des avant-bras, en particulier lors des mises en marche intempestives, des arrêts anormaux suite à une rupture d’énergie ou lors des nettoyages par exemple.
Risques liés aux manutentions
Le port de lourdes charges (transport du métal fondu...), les contraintesposturales exigeantes du rachis lors des moulages et démoulages, sont à l’origine d'accidents de travail concernant la colonne vertébrale (dorsalgies, lombosciatiques).
Autres risques physiques
Chutes de plain pied sur sol glissant, inégal ou encombré, projections de ferraille dans les yeux, troubles musculo-squelettiques causés par les activités en station debout prolongée, s'effectuant dans des postures complexes et avec des gestes répétitifs ou dans des espaces confinés notamment pour la réfection des fours, électrocution par contact direct, niveaux sonores élevés exposant les opérateurs de fonderie à des risques de troubles auditifs, pouvant entrainer à la longue une surdité professionnelle... - Risques d’incendie et d’explosion en fonderie
La vaporisation d’eau lors des opérations de transfert du métal en fusion exposent à un risque d'explosion : en effet, le contact d’objets humides et a fortiori d’eau avec un bain de métal en fusion peut provoquer des projections explosives de métal liquide, avec risque de propagation d’un incendie (d’où l’impératif de séchage des charges introduites, des poches et de l'outillage, et d’une zone de coulée exempte de trace d'eau).
Les mesures de prévention des risques dans les fonderies
Les ateliers des fonderies doivent faire l’objet d’une analyse poussée des risques pour permettre la rédaction du Document Unique de Sécurité (Décret du 5 novembre 2001) en appréciant à la fois l’environnement matériel et technique (outils, machines, produits utilisés) et l’efficacité des moyens de protection existants et de leur utilisation selon les postes de travail.
Les analyses de risques sont confiées à des spécialistes de la sécurité au travail (hygiéniste, ingénieur sécurité). Les rapports d’intervention et de maintenance seront aussi intégrés à la documentation de sécurité au travail de l’entreprise et communiquées au médecin du travail et au CHSCT.
Les salariés doivent être aussi informés à propos des produits dangereux mis en œuvre et formés aux pratiques professionnelles sécuritaires.
La prévention la plus efficace est la prévention primaire avec la mise en place de technologies qui permettent des actions sur les produits (suppression ou emploi de produits de substitution de moindre impact potentiel sur l'homme) et/ou des actions sur les procédés (emploi de matériels ou de machines supprimant ou limitant au maximum les impacts, par de très faibles rejets atmosphériques, par de bas niveaux sonores...).
La prévention collective implique l’utilisation de systèmes de fabrication isolés et automatisés et de dispositifs mécaniques comme l’extraction de poussières et de vapeurs qui permettent de réduire l’exposition des travailleurs, en particulier lorsque l’on ne peut pas remplacer des produits chimiques dangereux par d’autres pour des raisons techniques.
Enfin, le port d’équipement de protection individuel (combinaison, gants, chaussures et lunettes de protection, masques...) est obligatoire pour réduire le risque d’exposition non totalement éliminé par les mesures de protection collectives, ainsi que la présence d’installations et de matériel de premier secours.
- L’identification, la suppression / substitution des produits les plus toxiques
La première étape consiste à repérer en particulier les agents chimiques cancérogènes ou dangereux dans le cadre de l'évaluation des risques du Document Unique de Sécurité (DUS).
Les Fiches de Données de Sécurité (FDS), obligatoires pour tout produit chimique dangereux, comportent les renseignements relatifs à la toxicité des produits, donc notamment leur caractère cancérogène éventuel.
Si la substitution s’avère techniquement impossible, des actions par exemple comme l’abaissement de la teneur en formaldéhyde dans la résine, un mélange optimisé durcisseur/catalyseur pour limiter le relargage de gaz, permettent de réduire les risques. - Une ventilation des lieux de travail adéquate
La ventilation et l’aération des lieux de travail jouent un rôle essentiel pour limiter la concentration de l'ensemble des vapeurs dans l'air ambiant et les évacuer des lieux de travail, de façon à respecter les valeurs limites fixées par les réglementations et éviter ainsi les conséquences sur la santé des travailleurs. On procède par ventilation générale des ateliers et par aspiration continue à la source aux postes de travail.
La ventilation mécanique générale, extracteur d’air pour l’aspiration des vapeurs, doit assurer un renouvellement d'air en permanence afin de limiter les risques pour la santé, en évitant l’accumulation de vapeurs nocives et explosives, par extraction et soufflage : l'air est transporté dans le local par un ventilateur de soufflage et extrait du local par un ventilateur d'évacuation. L’extraction de l'air se fait grâce à un système de collecte par ces ventilateurs et des gaines de diffusion, réseau de conduits jusqu'aux filtres et aux épurateurs dans l'installation d'air soufflé qui permettent de nettoyer l'air, puis de l’évacuer à l'extérieur par rejet dans l'atmosphère.
Les composants aérauliques comme les ventilateurs, les conduits doivent être accessibles et faciles d’entretien et de nettoyage. En particulier, les réseaux s’encrassent rapidement avec de filtres hors d’usage, une évacuation des condensats obstruée... L'entretien régulier du système de ventilation (nettoyage des conduits d'extraction, changement des filtres) est une condition indispensable de bon fonctionnement.
Ces dispositifs doivent être complétés par une ventilation avec extraction localisée des vapeurs, des fumées et particules métalliques, brouillards d'huile ... ou sur les équipements avec filtres, épurateurs ou autres collecteurs de poussières : par exemple, dispositif d'extraction des machines de noyautage et de moulage, dispositif de captage sur la tête de malaxeur, évacuation des gaz de combustion et des fumées émises par les fours de fusion ...
Pour mesurer l’efficacité des installations de ventilation, la mesure périodique des agents chimiques par prélèvements d'atmosphère et analyses des vapeurs, gaz, poussières est importante.
La valeur limite correspond à sa concentration dans l’atmosphère dans laquelle une personne peut travailler pendant un temps donné sans risque d’altération pour sa santé.
La Valeur Limite d’Exposition (VLE) est la concentration maximum à laquelle un travailleur peut être exposée au plus pendant 15 mn sans altérations physiologiques : ce critère a pour but d’éviter les effets immédiats sur l’organisme.
La Valeur Limite Moyenne d’exposition (VME) est la limite d’exposition d’un travailleur pour une exposition régulière de 8h par jour et de 40h par semaine : ce critère a pour objectif d’éviter les effets à long terme sur l’organisme.
Par exemple : plomb 0,1 mg/m3 sur 8 heures ; 0,1 mg/m3 pour la silice cristalline sous forme de quartz et 0,05 mg/m3 pour la silice cristalline sous forme de cristobalite ; pour les fibres céramiques réfractaires 0,1 fibre par cm3 sur 8 heures.
La norme EN 481 concerne l’échantillonnage de poussières ou d’aérosols sur les lieux de travail et donne les caractéristiques des instruments à utiliser pour déterminer les concentrations.
Les mesures et analyses peuvent être faites par l’employeur ou par un laboratoire extérieur et le respect des valeurs limites doit être vérifié au moins annuellement.
Si la valeur limite d’exposition est dépassée, cela permet d’imposer un arrêt temporaire d'activité pour remédier à la situation, puis il faut réaliser un nouveau contrôle sans délai.
Ces rapports d’analyses métrologiques, d’intervention et de maintenance seront intégrés à la documentation de sécurité au travail de l’entreprise (Document Unique de Sécurité).
Pour compléter la prévention, des détecteurs de CO portatif ou fixe permettent un avertissement précoce du danger. - L’utilisation de machines et équipements adaptés
Le process des grandes fonderies industrielles est mécanisé et automatisé, ce qui réduit considérablement les risques thermiques, physiques (manutention, coupures...) et acoustiques. Toutefois, des incidents dans l’automatisation des opérations, des fuites, nécessitent des interventions de maintenance qui restent dangereuses. Par ailleurs, dans l’artisanat d’art, les petites séries, les pratiques sécuritaires sont beaucoup moins mises en œuvre et maîtrisées.
La protection contre les risques thermiques nécessite une bonne isolation thermique et l’inaccessibilité des parties chaudes des installations en installant des écrans thermiques, le confinement des machines de noyautage et de moulage, l’encoffrement des machines de grenaillage et décochage, des cabines d'ébarbage ventilées...
Toute machine doit porter les avertissements, signalisations et dispositifs d’alerte indispensables pour assurer la sécurité des travailleurs afin de supprimer ou réduire au minimum les risques de coupure, d’entraînement, d’écrasement, de cisaillement. Cette identification doit être réalisées par des pictogrammes et couleurs normalisées. Les éléments de travail doivent être disposés, protégés, commandés ou équipés de façon telle que les opérateurs ne puissent atteindre la zone dangereuse (carters de protection des organes en mouvement...).
Les panneaux de signalisation seront choisis et disposés de façon à être perçus et compris facilement sans ambiguïté. Chaque machine doit être munie d’un ou plusieurs dispositifs d’arrêt d’urgence et en cas d'ouverture clairement identifiables, accessibles et en nombre suffisant, permettant d’éviter les situations dangereuses en train de se produire. Les machines et équipements doivent être conçues et fabriquées de façon à ce que les émissions sonores soient réduites au niveau le plus bas possible en application d’une directive européenne 2003/10/CE du 6 février 2003 concernant les prescriptions minimales de sécurité et de santé relatives à l'exposition des travailleurs aux risques dus aux agents physiques liés au bruit.
Par le choix ou l’achat de machines et par l’utilisation de procédés silencieux, les émissions sonores peuvent être maintenues à un bas niveau.
Les machines bruyantes doivent être munies de capots insonorisants et pour réduire les bruits transmis par les sols et les structures, des blocs anti-vibrations peuvent être placés entre la machine et la surface d’appui.
En ce qui concerne les locaux, les réflexions sur les murs entraînent une augmentation du niveau sonore dans le local et des mesures préventives de correction acoustique comme la mise en place d’un plafond ou faux-plafond absorbant, de cloisons amovibles recouvertes de produit anti-réverbérant à proximité des installations, réduisent à la fois le niveau sonore et protègent les postes de travail avoisinants.
Les installations électriques doivent être conformes aux normes de sécurité : mise à la terre appropriée de l'équipement pour dissiper et diriger à la terre en toute sécurité les charges électriques accumulées, protection contre les contacts avec les masses mises accidentellement sous tension par un dispositif de coupure automatique en cas de défaut d’isolement et utilisation de disjoncteurs différentiels 30 mA de grande sensibilité...
Le respect des recommandations des constructeurs et un entretien régulier des installations sont des éléments essentiels pour limiter les risques accidentels et pour prévenir des émanations.
Ainsi, l’utilisation et l'entretien des machines doivent être effectués par un personnel qualifié, spécifiquement formé.
Des machines utilisées de manière non conforme ou mal entretenues et non vérifiées périodiquement créent un risque supplémentaire : par exemple, vérification de bon état du mécanisme de basculement des poches...
Des sols exempts de trous ou d'aspérités, avec des revêtements antidérapants, un drainage satisfaisant et des caillebotis qui évitent le dépôt de liquides, diminuent les risques de glissades et chutes de plain-pied : les sols doivent être de plus nettoyés régulièrement et tout produit accidentellement répandu, lors d’une fuite ou déversement, immédiatement épongé. - Un stockage des produits chimiques rigoureux
Le stockage des produits chimiques présente des risques tels que l’incendie, l’explosion, le risque de chute ou de renversement ou de détérioration d'emballage ... Toutes ces caractéristiques rendent nécessaire, outre les précautions lors de leur emploi, l’aménagement de locaux de stockage, avec des rayonnages métalliques, des planchers et des palettes normalisées, des armoires de sécuritépour petites quantités pour le stockage de produits inflammables, armoires avec étagères de rétention, matériels de stockage avec bacs rétention pour prévenir et maîtriser les fuites accidentelles de liquides polluants. La réduction des risques existants passe par une réflexion sur la structure du local, sur les modalités de rangement et sur les incompatibilités entre les produits. Des procédures de stockage non adaptées peuvent entraîner une fragilisation des emballages à l'origine de fuites ou de ruptures accidentelles, de pollution, de réactions dangereuses ou d'accidents ou induire une modification ou une dégradation des produits qui le rendent plus dangereux car ils peuvent libérer des vapeurs inflammables ou nocives.
L’empilement doit être stable et sa hauteur ne doit pas affecter l’intégrité des emballages.
Le stockage des bidons et autres sacs ou récipients, doit se faire dans un local ventilé par un système de ventilation mécanique, à l'abri de la chaleur et de l'humidité, et tous les conteneurs de produits chimiques doivent toujours être bien refermés.
L'installation électrique du local de stockage est à réaliser avec du matériel utilisable en atmosphère explosible.
Une bonne tenue des sols, imperméables et incombustibles, des locaux de stockage est essentielle pour éviter l’accumulation des matières déversées.
L’interdiction de fumer dans les locaux doit être absolument respectée et signalée de manière apparente (de même que toutes les autres consignes de sécurité).
Il faut stocker les plus faibles quantités de produits possibles car le risque d'incident ou d'accident croît avec la durée et le volume de stockage.
Il faut régulièrement vérifier les zones de stockage des produits chimiques utilisés dans les procédés, afin de repérer les fuites éventuelles. - Le respect des règles d’hygiène
Une bonne tenue des sols des locaux par aspiration ou par un procédé à l’humide (jet d’eau ou système eau/vapeur), est essentielle pour éviter l’accumulation de déversements et de poussières sous ou autour des machines. Les déversements peuvent créer un danger de glissement et par conséquent doivent être nettoyés immédiatement.
Des mesures complémentaires d’hygiène des locaux doivent être mises en œuvre tel le nettoyage régulier des machines et des parois de l’atelier à l’aide d’un aspirateur industriel adapté avec un filtre absolu qui ne disperse pas les poussières dans l’air (pas de soufflette à l’air comprimé, ni balayage).
Des lavabos, postes de rinçage oculaire et des douches de sécurité doivent se trouver à proximité des postes de travail. Celles-ci permettent les mesures d'hygiène générale : lavage des mains fréquent avec moyens adaptés, douche en fin de poste... En effet, le respect des règles d’hygiène s’étend aux comportements individuels : ne pas avoir les mains sales afin de ne pas ingérer par inadvertance un produit toxique et ne pas manger sur le lieu de travail.
Le personnel doit avoir à sa disposition des vestiaires et des sanitaires correctement équipés et en nombre suffisant. Des vestiaires doubles doivent être mis à la disposition des travailleurs : l’entreposage des tenues de travail doit avoir lieu à l’abri de la poussière et des souillures (le rangement des tenues de ville et des tenues de travail doit être séparé).
Des procédures de travail en ambiance chaude doivent être édictées et respectées de manière à réduire la contrainte thermique : absorption en quantité suffisante d’eau et de boissons renfermant des sels minéraux, rythme travail-repos aménagés en zone tempérée. - Le port d’équipements de protection individuel adéquat
Les équipements de protection individuelle sont nécessaires pour réduire le risque d’exposition non totalement éliminé par les mesures de protection collectives précédentes : gants, vêtements de protection, chaussures et lunettes de sécurité, différents et adaptés à la tâche effectuée.
S’il y a possibilité de contact avec la main lors des transvasements de produits chimiques par exemple, il s’avère indispensable de porter des gants de protection adaptés au produit manipulé : il n'existe pas de gant de protection universel. Le type de gants conseillé, imperméables, à longues manchettes, pour éviter la pénétration des produits à l’intérieur, doit être adapté aux différents produits manipulés selon leur composition qui figure sur la Fiche de Sécurité (FDS). Des gants appropriés doivent être aussi utilisés pour éviter les coupures aux mains, d’autres pour la protection contre la chaleur ainsi que des manchettes en isolant thermique.
Des vêtements ignifugés de protection contre la chaleur, tablier, lunettes de sécurité avec verres filtrant les infrarouges ou écran facial de protection complètent la protection pour les travailleurs exposés à la chaleur.
En cas d’urgence ou pour des travaux exceptionnels d’entretien de courte durée, si le système de ventilation ne suffit pas à empêcher l’accumulation de vapeurs ou de poussières, un appareil de protection respiratoire adéquat doit être fourni pour éviter l’exposition à une concentration élevée : masque à cartouche FFP3 avec un filtre adapté au produit.
De même, des protections auditives peuvent être recommandées pour compléter les mesures collectives qui s’avéreraient insuffisamment efficaces.
Des postes de rinçage oculaire et les douches de sécurité doivent se trouver à proximité des postes de travail pour ôter les projections de poussières ou autres corps étrangers dans les yeux. - La surveillance médicale
Pour les fondeurs exposés aux poussières de métaux lourds, aux agents cancérogènes, au bruit, et travaillant de nuit, il faut réaliser des visites médicales régulières dans le cadre d’une surveillance médicale renforcée :
- Tests respiratoires (spiromètre) à l’embauche pour détecter une déficience des fonctions pulmonaires et tous les 2 ans pour dépister l’apparition des troubles respiratoires.
- Radiographie thoracique si nécessaire, épreuves fonctionnelles respiratoires (EFR) conseillées,
- Audiogramme si nécessaire.
- Analyse annuelle du taux de plomb (plombémie) dans le sang
- Interdiction d'exposition des femmes enceintes ou des femmes allaitant à des travaux les exposant au plomb métallique ou à ses composés.
- Généralement, il y a un long délai entre l'exposition et le diagnostic d’un cancer professionnel (en général au moins 10 ans et jusqu'à 50 ans) ce qui nécessite une traçabilité au travers de la rédaction d’une fiche d'exposition et d’une surveillance médicale régulière, à visée de dépistage, réalisées par le médecin du travail.
A sa sortie de l’entreprise, le travailleur exposé doit recevoir une attestation d’exposition qui lui permettra de continuer à se faire suivre médicalement. La reconnaissance d'un cancer professionnel est importante, car elle ouvre droit à une réparation intégrale du préjudice subi pendant l’arrêt de travail (indemnisation et gratuité des soins) et au-delà s’il y a des séquelles (capital ou rente d’incapacité).
- Le dossier médical doit stipuler la nature du travail effectué, la durée des périodes d'exposition et les résultats des examens médicaux. Ces informations sont indiquées dans l'attestation d'exposition et le dossier médical doit être conservé 40 ans après la cessation de l'exposition.
- Suivi post professionnel (article D. 461-25 du code de la Sécurité sociale) : quand le salarié n'est plus exposé ou part à la retraite, ce suivi permet d'assurer pour les cancers professionnels qui se déclareraient après, une réparation du dommage subi. - La formation et l’information du personnel
La formation, par un organisme agréé, sur les dangers des produits utilisés et sur les moyens de se protéger, est indispensable : par exemple, comprendre les étiquettes du contenant des produits, informer sur le risque potentiel de maladies pulmonaires et sur les moyens de les prévenir, connaître l’attitude à adopter en cas de fuite ou de déversement accidentel, savoir utiliser les E.P.I adéquats, formation aux premiers secours et incendie, formation PRAP (Prévention des Risques liés à l'Activité Physique)...
Pour aller plus loin
- Recommandation R456 de l’Assurance Maladie : Risques chimiques en fonderie, 12 pages
- INRS : Les ateliers de moulage de pièces en alliage de cuivre, n° ED 921, 72 pages, 2004
- INRS : Postes de décochage en fonderie, n° ED 662, 24 pages, 2003
Juin 2012
Laissez un commentaire
Votre adresse de messagerie ne sera pas publiée.
Ces dossiers pourraient vous intéresser
Identification HSE
Créer mon compteNos rubriques
- Livres et édition
- Fiches Métier
- Materiel pédagogique
- Conseils
- Réparation matériels ATEX
- Travail en hauteur
- Sauveteur Secouriste du Travail (SST)
- Risque chimique
- Sécurité BTP
- Habilitations électriques
- Port des EPI
- Incendie - Explosion
- Gestes et postures - PRAP
- Conduite d'engins
- Prévention routière
- Formation continue à la sécurité
- Formation initiale à la sécurité
- Experts agréés auprés des CSSCT
- Formation de la CSSCT