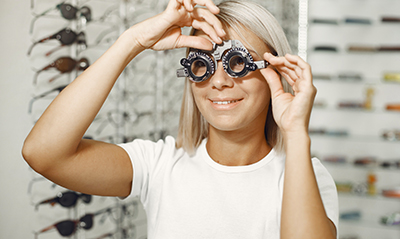
Les centres de distribution (ou plates-formes logistiques), sont des entrepôts qui gèrent les flux de marchandises depuis leur lieu de production jusqu'aux magasins de détail ou aux clients finaux. Les taches de la chaine logistique sont confiées aux magasiniers-caristes et aux préparateurs de commandes. Ces métiers sont exposés à des risques provenant des nombreuses manutentions manuelles et déplacements dans les magasins, des dangers de l'utilisation de chariots automoteurs, de transpalettes, de rayonnages métalliques ... le tout dans une organisation soumise à des impératifs de rendement.
Les centres de distribution (ou plates-formes logistiques), sont des entrepôts qui gèrent les flux de marchandises depuis leur lieu de production jusqu'aux magasins de détail ou aux clients finaux, recevant des marchandises en gros volume, les stockant et les réexpédiant en petits lots : approvisionnement des rayonnages, stockage sur palettes, préparation, emballage et livraison des marchandises pour l'expédition sont des taches de la chaine logistique confiées aux magasiniers-caristes et aux préparateurs de commandes. Ces métiers sont exposés à des risques provenant des nombreuses manutentions manuelles et déplacements dans les magasins, des dangers de l'utilisation de chariots automoteurs, de transpalettes, de rayonnages métalliques permettant le transport et le stockage des palettes ainsi que du stress de la préparation de commandes (notamment avec le système du « voice picking »), le tout dans une organisation soumise à des impératifs de rendement.
Les mesures préventives portent sur :
- L'analyse des flux de circulation interne et la mise en place un plan de circulation, qui limite les risques de collision entre véhicules et heurts avec des personnes ou des obstacles, de chutes de charges, …
- L'éclairage, la signalisation et l'entretien des voies de circulation,
- L'ergonomie, la vérification du bon état des engins de manutention et de la formation de leurs conducteurs,
- La bonne conception et installation, l'entretien régulier des équipements de stockage (racks ou palettiers) et l'usage adapté aux charges stockées pour préserver la sécurité des personnes, piétons ou conducteurs d'engins, qui travaillent près de ces structures.
- L'utilisation d'outils adaptés (dérouleurs de filmage, cutters anti-coupures..).
- La réduction de l'intensification et la répétitivité des taches, le souci de laisser une latitude décisionnelle aux opérateurs, la formation aux bons gestes et postures.
Nota : ce dossier ne traite pas des risques sur les quais de réception et d'expédition. Voir à ce sujet dans OFFICIEL-PREVENTION le dossier suivant : la sécurité aux quais de transbordement dans Protections collectives - Organisation – Ergonomie > Manutentions
Les principaux risques dans les centres de distribution
La gestion optimale des chaînes logistiques, ou "supply chain management", entraine la création de nombreux et vastes centres de distribution, dont l'importance n'a cessé de croitre, avec une main d'œuvre, elle-aussi en augmentation, soumise à un taux de sinistralité au travail élevé : l'activité logistique, avec le BTP, est un des secteurs industriels les plus accidentogène.
Dans les entrepôts et magasins des plates-formes de distribution, les travailleurs les plus exposés aux risques d'accidents du travail sont les magasiniers-caristes et les préparateurs de commandes.
Les travailleurs intérimaires qui sont nombreux dans ce secteur sont encore plus exposés aux risques de ces accidents du travail du fait du manque d'information de cette main d'œuvre, de formation et de connaissances des lieux et des procédés qui augmentent ainsi leur vulnérabilité.
-le magasinier-cariste
Le magasinier-cariste effectue la réception et le stockage des marchandises sur les rayonnages métalliques, à l'aide de différents chariots automoteurs de transport et élévateurs. Le cariste conduit un chariot automoteur pour manutentionner des marchandises et approvisionner les stocks en gerbant en hauteur les palettes pour les placer sur les alvéoles de stockage.
Les déplacements des chariots pour les approvisionnements des stocks sont responsables de collisions entre véhicules et heurts avec des personnes ou des obstacles, de chutes de charges, et l'exposition aux vibrations des engins provoquent des traumatismes aux caristes. Par ailleurs, les rayonnages métalliques permettant un stockage de palettes (ou racks de stockage ou palettiers) sont largement utilisés dans tous les magasins et les entrepôts des centres de distribution…, car ce stockage en hauteur permet d'optimiser au maximum l'espace des locaux : ces structures sont sources de risques fréquents, soit du fait de chutes d'objets, soit d'effondrement total ou partiel de la structure par surcharge, mauvaise fixation ou entretien, par choc brutal d'un engin de manutention ou impacts répétés des déposes de charge.
-Le préparateur de commande
Le préparateur de commandes est le manutentionnaire qui compose une commande pour un client. A la réception des bons de commandes, il prélève les produits dans les stocks, les met sur palette et les déplace par exemple sur des diables ou des transpalettes manuels ou électriques, les emballe et les étiquète. Ces activités entrainent une gestuelle répétitive et des postures souvent contraignantes. Dans certains entrepôts ou les marchandises sont assez légères (produits pharmaceutiques…), des machines automatisées vont elles-mêmes chercher les produits en stock.
La préparation de commande peut se dérouler de deux manières différentes : le picking (préparation sur stock) ou le préparateur charge une palette de produits prélevés sur les rayonnages de stockage (racks) puis effectue le filmage, et l'éclatement (ou allotissement) ou le préparateur distribue sur des chariots spéciaux (rolls) les colis prêts à la livraison (gestion en flux tendu).
Il existe plusieurs modes de guidage : listing, terminal radio, « voice picking »…qui permettent d'organiser son travail et choisir son chemin de préparation de façon plus ou moins autonome.
Dans la méthode du « voice picking », ou préparation vocale assistée par ordinateur, un logiciel de gestion dicte aux préparateurs, munis d'un casque d'écoute, l'emplacement et la quantité des produits à charger sur les palettes avant leur emballage et l'embarquement sur les camions de livraison.
- Les risques de la manutention manuelle
Le développement général de l'activité des plateformes logistiques a accru fortement les accidents du travail liés aux manutentions manuelles ou aux ports de charges : les dangers sont liés à la nature des charges, au nombre excessif de manipulation et au mouvement : torsion, déplacement, soulèvement. Non seulement les risques d'accidents de travail concernent le dos (lombosciatiques, cervicalgies) mais aussi les membres supérieurs (tendinopathies des coudes et des épaules, syndromes du canal carpien des poignets) et inférieurs (entorses …) ou les extrémités (coincement des doigts …) et le vieillissement progressif des structures ostéoarticulaires peut aboutir à une inaptitude professionnelle, ce qui, de par leur fréquence et leur impact, tant médical que socioprofessionnel, constitue un problème majeur de santé au travail dans les centres de distribution.
La manutention manuelle est à l'origine de fréquents accidents du dos souvent dus à des postures incorrectes (à bout de bras, tronc penché en avant). Elle peut engendrer, tout comme la manutention mécanique, des contusions, des écrasements, des chutes. De plus, les surfaces anguleuses ou rugueuses, les chutes d'objets sont parmi les principales causes de blessures, de lacérations ou de contusions pendant le travail de manutention manuelle. Le travailleur peut également subir ces blessures s'il tombe ou s'il entre en collision avec des objets.
Certains facteurs peuvent aggraver la pénibilité de la manutention manuelle :
- Facteurs liés à la charge : poids, taille et forme de la charge ; charge située en hauteur ou à déposer en hauteur.
- Facteurs liés aux locaux de travail : espace de travail exigu, sol encombré, en mauvais état, glissant du fait des ruptures d'emballage ou fuites et déversements de liquides...
- Facteurs d'ambiance : ambiance froide (entrepôt frigorifique) ou chaude, intempéries, bruit
- Facteurs organisationnels : cadence rapide, gestes répétitifs, travail dans l'urgence, travail posté, travail de nuit.
Le filmage de la palette avec un rouleau de film étirable occasionne des efforts de traction, de torsion, de position tête en bas provoquant des contraintes sur le rachis et sur le système cardiaque et vestibulaire (vertiges). Les risques de troubles musculo-squelettiques (TMS) du banderolage sont aggravés si cette tâche est répétitive : les fréquentes alternances de postures entre les positions baissé, courbé et redressé provoque une augmentation du rythme cardiaque et une hypotension orthostatique sur l'oreille interne.
L'ouverture (ou la réouverture) de cartons et d'emballages avec des cutters est susceptible de provoquer des accidents aux mains, des coupures plus ou moins profondes d'un doigt ou d'un membre, des perforations... - Les risques de la circulation interne
Les risques concernent les collisions entre véhicules, les heurts de véhicules sur des travailleurs ou des obstacles, des freinages ou virages brusques d'engins qui mènent à la chute de la charge sur des personnes.
Les dangers concernent donc non seulement les conducteurs d'engins (caristes) mais également tous les travailleurs qui se trouvent à proximité, qui peuvent être heurtés par l'engin ou sa charge du fait de l'inattention, du manque de visibilité, ...
Les situations à risques tiennent aux voies de circulation, aux engins, à l'organisation des flux circulatoires et aux comportements humains : tous ces facteurs agissent de façon autonome mais aussi inter-dépendamment, et à chaque modification apportée à l'un d'entre eux, le risque d'accident est susceptible de changer lui aussi.
- Les voies de circulation
La largeur et la géométrie des voies de circulation, sont parfois insuffisantes et/ou peu pratiques (virages trop serrés, rétrécissements, dénivelés…), des angles morts existent, les espaces sont trop étroits ou mal adaptés pour réaliser des manœuvres,…
La circulation sur les voies peut être perturbée par des obstacles permanents (poteaux, piliers, tuyauteries…) ou temporaires (palettes, outils, emballages non rangés...), qui obligent à des contournements délicats ou provoquent des heurts.
Les sources d'éclairage mal positionnées entrainent des zones d'ombre ou à contre jour. Une assise du sol peu solide, inégale, glissante provoquent des embardées et cahots. Des aires de circulation des piétons et des engins non ou mal matérialisées par marquage au sol des zones de cheminement, l'absence de signalisation adéquate génèrent un manque d'information très préjudiciable à la sécurité.
- Les engins
Les engins utilisés dans les centres de distribution sont variés : chariots divers de manutention et de levage, transpalettes manuels ou électriques… La diversité de leurs vitesse, poids, gabarit, manœuvrabilité font de leur coexistence un facteur de danger. Le mauvais état de ces véhicules (freins, pneumatiques, direction, feux de signalisation, éclairage, moyens de calage, avertisseurs sonores ou lumineux), par défaut d'entretien et de maintenance, est un facteur d'accident. De même que l'absence ou la dimension insuffisante des rétroviseurs.
- Les facteurs humains et comportementaux- Le comportement des magasiniers et des conducteurs d'engins de manutention est fondamental car les dimensions psychologiques ou cognitives modifient leur perception du risque, augmentant la probabilité d'erreurs ou d'omissions humaines de toutes sortes.
- Indiscipline : non-respect des règles et des procédures, de la signalisation, des priorités, des passages piétons, stationnement sauvage, vitesse excessive, cheminement hors des zones prévues …
- Variabilité des critères d'aptitude des individus (morphologie, sexe, handicap, ancienneté dans l'entreprise, fatigue…).
- Organisation du travail générant précipitation, stress.
- Comportements addictifs : alcoolisme, drogues, médicaments psychotropes.
- Les risques des engins de manutention
- Le renversement latéral du chariot automoteur, les heurts avec un élément de bâtiment ou une structure de stockage (dont retour de volant lorsque la roue heurte un obstacle), la chute de la charge (principalement depuis les fourches ou en montant ou en descendant du chariot), l'exposition aux vibrations sont les risques les plus fréquent pour le cariste : il en résulte des traumatismes pouvant être graves, des troubles musculo-squelettiques induits par les contraintes posturales (rotation du tronc et de la tête) et des lombalgies liée aux vibrations. Le risque total dépend de la dose vibratoire excessive en instantané, mais aussi de la totalité de la dose vibratoire reçue au cours de la journée de travail et de la vie professionnelle.
- Si les transpalettes limitent les risques de blessures dues à un effort excessif dans les travaux de manutention, toutefois, le fait de tirer, de pousser et de manipuler un transpalette présente certains dangers, tels que : les doigts et les mains qui peuvent rester coincés (p. ex., entre le chariot et d'autres objets); les orteils qui peuvent être écrasés sous un chariot ; les pieds ou les jambes qui peuvent être heurtés par la chute de la charge … - Les risques des équipements de stockage
Tous les systèmes de stockage comportent des risques. Des rayonnages mal conçus et mal utilisés peuvent se révéler très dangereux car le personnel d'exploitation est exposé :
- aux chutes de charges sur des lieux de passage très fréquentés : lors des manutentions en hauteur, un colis mal arrimé sur une palette peut tomber sur les manutentionnaires ou sur les magasiniers et entrainer des blessures gravissimes. Les risques de chutes du matériel en raison des rayonnages trop hauts, non fixés ou surchargés peuvent entrainer des contusions corporelles sévères (écrasement des membres, traumatisme crânien, abdominal ou thoracique).
- aux heurts des engins de manutention qui peuvent frotter contre les structures entraînant, petit à petit, le décrochage de lisses ou entretoises, la déformation de l'installation ou pire, venir heurter les piliers des rayonnages et entrainer leur effondrement.
- à des charges qui peuvent être trop lourdes et le dépassement de poids prévu conduit à la déstructuration des alvéoles de rayonnages.
- à l'instabilité du rayonnage métallique : défaut de planéité ou d'horizontalité du sol, problème de calage ou de fixation, fissures formées dans les planchers de béton. - Les risques psychologiques
Les réponses organisationnelles à toutes les exigences de productivité se caractérisent dans le secteur de la logistique par une grande augmentation des pressions (réduction des erreurs, des casses, des délais, des manquants et des niveaux de stock) exercées notamment par les grandes surfaces de distribution alimentaires (GSA), de bricolage (GSB) ou d'habillement. La crainte d'erreurs dans la préparation des commandes soumise à des impératifs de rendement, le « voice picking », système de préparation de commandes assistée par ordinateur par système de reconnaissance et de guidage vocal, génère un stress permanent, aggravé par des facteurs organisationnels : cadences rapides pour augmenter la productivité, travail dans l'urgence, travail posté et de nuit (par exemple en messagerie). La flexibilité imposée avec des exigences d'horaires ajustés en fonction de la demande et le travail en horaires décalés, la disponibilité constante par le truchement du casque d'écoute, l'intensification de la charge mentale due aux nouvelles technologies informatiques, le travail effectué à flux tendu,… sont des facteurs de stress qui provoque à court et à long terme, une augmentation de la fréquence cardiaque, de la pression artérielle, entraînant de nombreuses conséquences psychosomatiques : atteintes physiques comme les troubles gastro-intestinaux, augmentation des accidents cardiovasculaires et accidents vasculaires cérébraux, céphalées et migraines, atteintes psychiques comme fatigue et irritabilité chroniques, troubles du sommeil et des conduites alimentaires (obésité), consommation accrue de médicaments anxiolytiques, d'alcool et de substances psychotropes…
L'isolement, l'absence d'autonomie, la perte d'identité, le repli sur soi sont des conséquences possibles du « voice picking » sur le préparateur de commandes : interaction constante entre le casque et le travailleur muni d'un kit mains libres pour les dialogues avec l'ordinateur, absence de communication avec son entourage, perte d'initiative ou marge de manœuvre sur son itinéraire, …Cette dépendance à la machine, si elle est ressentie comme excessive, est facteur de risque psychologique.
Les mesures préventives des risques professionnels des centres de distribution
Pour diminuer les risques professionnels dans les centres de distribution, il faut prendre une série de mesures préventives, ayant trait à la prévention organisationnelle (plan de circulation, règles et procédures…), technique (aménagement des voies et des locaux, entretien et ergonomie des engins, sécurité des équipements de stockage…) et psychologique (organisation, formation…), ainsi qu'à prévention individuelle (équipements de protection).
Au-delà de l'amélioration des conditions de travail et de la santé au travail des employés des centres de distribution, ces mesures entrainent une meilleure productivité du fait de la moindre démotivation, d'un turn-over et d'un absentéisme réduits (dont les taux sont élevés dans ce secteur d'activité).
Il convient d'évaluer les risques professionnels dans le centre de distribution et de rédiger le Document Unique de Sécurité en appréciant à la fois l'environnement matériel et technique et l'environnement managérial et organisationnel. La retranscription de cet état des lieux dans le Document Unique doit conduire à l'élaboration d'un plan de prévention correspondant aux risques identifiés, y compris pour les aspects psychologiques qui existent dans les centres de distribution et sont parfois négligés.
- Les mesures préventives organisationnelles
- - L'établissement d'un plan de circulation permet de déterminer le tracé des trajets effectués dans l'entreprise et leurs itinéraires et de lister les moyens de transport des marchandises et de déplacement des personnes. Cela permet d'identifier les zones critiques des circulations (croisements multiples, …), de prévoir des voies de décélération, d'accélération et ronds points giratoire, les zones de stationnement, l'emplacement des aires de chargement/déchargement, les zones interdites ou réservées à certains véhicules etc.
Le plan de circulation est à la fois un outil technique qui permet une vision globale de la circulation dans l'entreprise, mais aussi un outil d'information auprès du personnel, des entreprises extérieures amenées à intervenir à l'intérieur de l'entreprise (sous-traitants, maintenance …).
- Règles de circulation
Les consignes générales de circulation interne doivent être intégrées au règlement intérieur de l'entreprise : règles sur les manœuvres de demi-tours, marches arrière, priorités de passage, limitation de vitesse, distances de sécurité etc. Le règlement intérieur permet aussi de mettre en place un véritable « règlement alcool et produits illicites » de l'entreprise et d'interdire cette consommation dans l'entreprise formellement pour tous les conducteurs et caristes pour leur sécurité et celle d'autrui. Le dépistage d'alcoolémie est autorisé pour autant que la liste des postes de travail concernés, le rythme et les conditions de pratique des contrôles soient incluses dans le règlement intérieur.
- Conditions de travail
Une saine gestion rend compatible la pratique avec les règles de circulation interne, qui ne l'est pas ou peu lorsque d'autres priorités apparaissent contraignantes à l'excès : délais impératifs à respecter, aires de stockages saturées, … La réduction des contraintes de manutention et des déplacements font partie des changements organisationnels qui contribuent automatiquement à diminuer les risques liés au transport interne : diminuer les distances entre les points à desservir, avec des chemins les plus courts possibles, réduction de la hauteur des palettes pour diminuer le travail des bras,… L'augmentation de la fréquence des pauses des pauses pour permettre des échanges et la restauration de marges de manœuvre pour le préparateur de commandes assujetti au « voice picking » sont nécessaires. La polyvalence permet aussi d'alterner les taches entre opérateurs (postes de réception ou d'expédition).- Les mesures préventives techniques
- - Dimensionnement des aires de circulation
Les allées de circulation doivent être nettement délimitées et dégagées de tout encombrement et obstacle, et de largeur suffisante.
- Equipement et entretien des aires de circulation- revêtement au sol à la résistance adaptée aux sollicitations, anti-dérapant, sans trous.
- éclairage approprié des différentes zones, bien positionné
- marquage au sol des zones de cheminement bien clair
- ouvertures recouvertes de plaques encastrées au raz du sol conformes à la norme
NF EN 124 - équipements d'aide à la visibilité (miroir) pour les zones aveugles
- suppression des obstacles et rectification des virages
- Confort thermique des locaux.
Il convient d'adapter l'aération, la ventilation et l'isolation thermique des locaux des entrepôts.
- Equipement et entretien des engins
La présence et le bon fonctionnement des équipements de sécurité des véhicules et engins est indispensable : éclairage, avertisseur sonore et/ou lumineux de recul, freins, pneumatiques, direction, moyens de calage, rétroviseurs, ceinture et arceaux de sécurité, bouclier, dosseret protège-tête adapté. Sièges ergonomiques suspendus et réglables et tapis de sol rembourré réduisant les transmissions de vibrations pour les chariots, roulettes en bon état pour les transpalettes sont aussi des facteurs de diminution des troubles musculo-squelettiques.
Les chariots automoteurs sont soumis à trois types de vérifications :- les vérifications lors de la mise en service,
- les vérifications lors de la remise en service après réparation ou accident (démontage, remontage ou modification pouvant remettre en cause la sécurité)
- Les chariots automoteurs doivent subir une visite générale périodique (à réaliser tous les 6 mois par un organisme compétent ou une personne qualifiée).
- La signalétique de circulation
Des pictogrammes de signalisation ou panneaux permettent d'aménager des cheminements sécurisés en attirant l'attention ou en signalant un danger spécifique à certains endroits (présence de produits dangereux stockés, repérage des obstacles …). Ils doivent être identiques au code de la route pour les cas les plus courants, avec un logo spécifique sinon.
L'efficacité de la signalisation dépend de son emplacement (endroit bien éclairé, facilement accessible) et doit être visible soit à l'accès à une zone pour un risque général, soit à proximité immédiate d'un risque déterminé ou d'un objet (poteau, tuyauterie…) à signaler. Une signalétique redondante ou excessive est à proscrire (Ex : nombre excessif de panneaux à proximité immédiate les uns des autres, signal lumineux à proximité d'une autre émission lumineuse,....).
- Les équipements de stockage doivent être conçus et mis en place de manière à pouvoir supporter les charges, à en empêcher la chute et l'effondrement des racks.
La sécurité des entrepôts dépend d'abord de leur conception, ensuite de leur utilisation.
Les règles de construction des entrepôts concernent l'implantation des voies de circulation, le dimensionnement et la structure des équipements de stockage adaptés au poids des matériaux à stocker, la qualité de la surface de fixation et du calage des piliers au sol, le bon éclairage des locaux.
L'accès entre les rayons doit être suffisant (largeur supérieure à 80 cm) pour la manutention des produits et l'inspection des stocks. La largeur des voies de circulation doit dépasser d'au moins 1 m la largeur des engins de manutention ou de la charge transportée (Exemple : largeur de chariot 1 m ; largeur minimale de l'allée 2 m).
On dispose des sabots de protection à la base des rayonnages, pour éviter les chocs des chariots de manutention. Chaque entrée de rayonnage indiquera les dimensions du support avec sa charge et la charge unitaire maximale par alvéole. La bonne utilisation des équipements de stockage repose sur une répartition des charges adéquate sur la surface de stockage. Car la stabilité du rayonnage dépend en effet, en grande partie, de la stabilité des produits stockés.
Il convient de contrôler les rayonnages, neufs ou existants de façon périodique suivant la norme NF EN 15635 : qualité du montage réalisé et des éléments de sécurité mis en œuvre, identification de tous les composants déformés ou impactés. Les visites annuelles de contrôle doivent être suivies d'opérations de remise en état et de remplacement de pièces hors d'usage.
-Les accessoires de sécurité des équipements de stockage
Il existe une large gamme d'accessoires pour assurer un stockage efficace des produits et la sécurité des personnes et destinés à l'aménagement des zones de transfert de marchandises.- les butées (ou arrêtoirs) de palettes se montent à l'arrière des rayonnages pour prévenir la chute des palettes et permettre un bon alignement sur les niveaux
- les cloisons grillagées anti-chutes qui répondent aux exigences de sécurité des racks à palettes et se fixent à l'arrière des racks à palettes pour protéger les allées de circulation des chutes de marchandises. Elles peuvent aussi servir à protéger les marchandises contre le vol. Les panneaux sont constitués d'un treillis soudé sur un cadre tubulaire pour obtenir une résistance optimale
- les filets de protection pour rayonnages
- les protections d'extrémités des porte-palette, protecteurs de poteaux et d'angle
- les barrières et rambardes de sécurité et balustrades garde corps
- Les bandes de signalisation ainsi que les bandes antidérapantes pour sécuriser les entrepôts et aires de passage.
- Les étiquettes adhésives permettant à l'opérateur de visualiser la charge admissible par niveau de stockage
-L'utilisation du chariot automoteur
- Prendre connaissance du site de travail et des instructions à respecter à chaque prise de poste ou avant chaque nouvelle tâche (état des sols, ponts de liaison, stabilité des stockages, etc.).
- Ne pas prendre un virage trop rapidement, ce qui tend à faire basculer le chariot
- Ne pas lever une charge supérieure à la capacité de l'appareil.
- Ne pas augmenter la valeur du contrepoids des chariots.
- Ne pas lever une charge mal équilibrée.
- Ne pas lever une charge avec un seul bras de fourche.
- Ne pas circuler avec une charge haute.
- Ne pas freiner brusquement
-L'utilisation du transpalette
- Avant levage, s'assurer que les palettes, plates-formes... sont appropriées aux charges à déplacer et en état de les supporter.
- S'assurer que les charges sont parfaitement équilibrées, calées ou amarrées sur leurs supports.
- S'assurer que la charge est stable et bien centrée sur le plateau ou les fourches, qu'elle ne dépasse pas du gabarit de l'engin et que le centre de gravité est le plus bas possible. Eviter les charges hautes qui masquent la visibilité vers l'avant (moins e 1,2 m).
- Engager les bras de fourche à fond sous les charges, ne jamais lever une charge avec un seul bras de fourche.
- Ne placez en aucun moment les mains ou pieds sous le transpalette.
- Ne laisser jamais un transpalette chargé en position de levage sans surveillance; abaisser toujours la charge au plancher.
- Utiliser les moyens de manutention manuels « au pas », c'est-à-dire à la vitesse de marche d'une personne (3 à 4 km/h), sans virage brusque et interdire formellement le transport de personnes.
-L'utilisation d'un dérouleur de filmage approprié
Les opérations de filmage manuel de palettes sont un facteur de risques pour les préparateurs de commandes non équipés d'un dispositif de filmage approprié qui, grâce à son ergonomie, permet de limiter les efforts physiques répétitifs et contraignants.
-L'utilisation d'outils anti-coupures
L'employeur doit fournir des outils de sécurité destinés au déconditionnement à lame automatiquement rétractable. En ce qui concerne le cutter coupe-film pour couper les films plastiques épais, des mécanismes de sécurité avec dispositif de retrait automatique protègent les mains et le corps d'un faux mouvement de la lame.
• Les mesures préventives individuelles
- L'utilisation des protections individuelles adaptées aux taches exécutées (vêtements de travail, chaussures de sécurité, gants, casques, port éventuel d'une ceinture lombaire et d'une protection auditive ….) est indispensable.
- Pas de boissons alcoolisées ni de prise de drogues ou de médicaments pouvant altérer la vigilance.
- Formations- Les conducteurs d'engins de manutention doivent avoir reçu une formation adéquate et être en possession de l'autorisation de conduite délivrée par le chef d'établissement (Article R 233-13-19 du code du travail). Bien que non obligatoire, le Certificat d'Aptitude à la Conduite d'Engins en Sécurité (CACES) est fortement recommandé pour valider les compétences requises.
- La formation aux bons gestes et postures en manutentions manuelles est au cœur du dispositif de prévention : la mise en place de formations PRAP (Prévention des Risques liées aux Activités Physiques) est un des moyens permettant de lutter contre tous les troubles musculo-squelettiques dus à des positions articulaires inadéquates, en appliquant les principes de base de sécurité physique et d'économie d'effort.
- Pour le personnel intérimaire, une information minimale sur les risques et les moyens de les prévenir (notamment pour les dorsalgies, tendinites, coupures, …) doit être prévue, à la fois dans le cadre de leur intégration, puis lors d'un suivi particulier et d'un encadrement adapté à leur profil.
Octobre 2012
Partagez et diffusez ce dossier
Laissez un commentaire
Votre adresse de messagerie ne sera pas publiée.
Les avis des internautes
23/07/2022