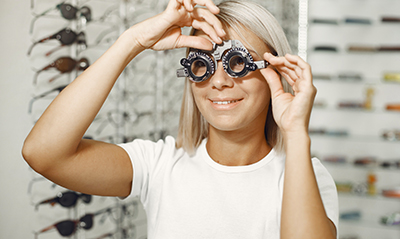
L’industrie des briques et des tuiles associe les risques liés à l’extraction de l’argile dans une carrière située à proximité immédiate, au transport sur le site de production, aux sources de nuisances des procédés de broyage des terres, de moulage, de pressage, d’emballage ... et de cuisson dans des fours à température élevée.
L’industrie des briques et des tuiles associe les risques liés à l’extraction de l’argile dans une carrière située à proximité immédiate, au transport sur le site de production, aux sources de nuisances des procédés de broyage des terres, de moulage, de pressage, d’emballage ... et de cuisson dans des fours à température élevée : bruit, émissions de gaz et de poussières fines et agressives, nombreuses manutentions manuelles et mécaniques, collisions entre engins et piétons, happements, coincements avec des machines, brulures.
Par des mesures de prévention collectives appropriées, on peut réduire toutes ces expositions et diminuer fortement les risques professionnels dans les briqueteries et tuileries.
De plus, le travail des briquetiers et tuiliers exige que soient respectées scrupuleusement les consignes sur les moyens de protection individuelle (port du casque, gants, chaussures et masque de protection...).
Par ailleurs les mesures de formation à la sécurité et d’information sont indispensables, particulièrement en ce qui concerne la conduite d’engins.
Les principaux risques dans les briqueteries et tuileries
Le matériau de base est l’argile, terre limoneuse et schisteuse, extraite dans une argilière : on ajoute à la glaise des adjuvants (schiste pulvérisé, sable, sciure de bois, oxyde de manganèse, dégraissant ...) afin d’obtenir les qualités souhaitées (porosité, couleur, résistance ...).
Les différentes opérations de production des briques et tuiles sont similaires :
- Extraction de l’argile
L'exploitation de l’argilière, généralement très proche du lieu de production, s’effectue dans une carrière à ciel ouvert, à l’aide d’engins lourds (pelle hydraulique, chargeur, dumper, ...) et l’argile est transportée dans des camions, godets, convoyeurs à bande jusqu’au site de préparation des terres.
- Préparation du mélange
Broyage et le malaxage de l’argile, puis le dosage et le mélange avec les adjuvants (notamment le sable) permettent d’homogénéiser et de d’obtenir une granulométrie optimale avant le façonnage.
- Façonnage
La mise en forme est mécanisée et se fait soit dans des moules (moulage), soit par extrusion (étirage).
Après avoir été stocké dans une cave à terre, le mélange malaxé et humidifié passe alors dans une mouleuse, ou une étireuse et une découpeuse, ou une presse pour être façonné.
- Séchage et cuisson
Dans un four tunnel au gaz naturel, la fournée est chargée sur des wagonnets qui parcourent un tunnel rectiligne et passent successivement par les zones de séchage, de cuisson et de refroidissement : le séchage (à 150 °C) permet de réduire le taux d’humidité, puis un cycle de cuisson avec un échauffement progressif jusqu’à une température maximale entre 900 °C et 1200 °C selon les produits suivi d’un lent refroidissement aboutit à des briques ou des tuiles finies.
- Palettisation
Après la sortie du four, les supports de cuisson sont dépilés et les tuiles passent dans une cabine de tri sur un tapis roulant pour être inspectées.
Les produits sont empilés en paquets, mis en palette houssée : la housseuse recouvre les palettes d’un film plastique thermocollé.
Dans toutes ces phases de production de briques et tuiles, les travaux exposent les briquetiers et tuiliers à de nombreux risques professionnels.
- Les risques thermiques dans les briqueteries et tuileries
Lors de la production des briques et des tuiles, la température dans le four va de 900 à 1200 °C environ selon les applications : de ce fait, les locaux des ateliers sont donc particulièrement exposés à l’énergie rayonnante des infrarouges, aux températures élevées et aux risques de brûlures thermiques, avec de plus des fluctuations de température. Le contact avec des surfaces chaudes notamment pendant les périodes de montage, réglage et maintenance sont les principales sources de risque thermique.
Le contact direct de la peau avec des surfaces chaudes ou des matériaux en sortie de four peut bien entendu d’abord provoquer de très graves brûlures cutanées.
Mais la proximité d’une source de chaleur peut aussi entrainer des céphalées, hypersudation, tachycardie, hypotension et, conjuguée à des températures de l’air élevée, provoquer des malaises dus à la déshydratation et des troubles circulatoires. Au-delà de 25 oC, l'inconfort se fait ressentir avec, de plus, toutes les conséquences psychologiques que cela peut avoir sur la précision des gestes, la vigilance et donc la sécurité (diminution des capacités de réaction, irritabilité, agressivité). - Les risques chimiques dans les briqueteries et tuileries
Les substances entrant dans la composition de la brique et de la tuile sont très nombreuses et les fumées et les poussières provenant des matières premières en suspension (silice, poussières alcalines, fumées de métaux lourds et d’oxydes métalliques, etc.) exposent les briquetiers et tuiliers à des dangers d’affections respiratoires, surtout lors de la cuisson qui occasionne des émissions atmosphériques abondantes. Mais aussi, des particules minérales solides en suspension dans l’air sont produites dans les argilières en continu et à tous les points du traitement : chargement, convoyage, roulage des camions, broyage, ..., et, par temps sec, ensoleillé et/ou venté, ce phénomène est accentué.
- Les poussières de silice sont émises lors de nombreuses opérations (l’argile peut contenir de 10 à 50% de silice) : ces émissions peuvent induire une irritation des yeux et provoquer l’apparition de bronchites chroniques et des particules de silice cristalline inhalées de façon intense et fréquente peuvent générer des cancers broncho-pulmonaires et la silicose, une pneumoconiose fibrosante se traduisant par un essoufflement à l’effort (dyspnée) et de la toux au début, jusqu’à une déficience respiratoire très grave et une insuffisance cardiaque.
- Lorsque des particules de poussière irritantes se logent dans le nez, elles peuvent causer une rhinite allergique ou une inflammation de la muqueuse nasale.
Certaines particules très fines réussissent à traverser la cavité nasale et à s'attaquer à la trachée et aux poumons, ou elles engendrent une inflammation des muqueuses de la trachée (trachéite) ou des bronches (bronchite), mais surtout parviennent à atteindre les alvéoles pulmonaires, et s’y accumuler si l’intensité ou la fréquence d’exposition dépasse le seuil d’élimination naturelle du corps par le mucus (biopersistance). Les poumons sont alors constamment exposés aux risques liés à la poussière respirée et l'inhalation excessive de poussière peut causer une pneumopathie.
- Le Code du Travail fixe un seuil de danger de concentration de poussières inhalables à ne pas dépasser à 10 mg/m3. Des valeurs limites d’exposition professionnelle VLEP réglementaires contraignantes sont fixées dans le Code du travail (article R. 4412-149 et décret du 10 avril 1997). La concentration moyenne en silice cristalline de l'atmosphère inhalée par un travailleur pendant une journée de travail de 8 heures ne doit pas dépasser 0,1 mg/m3 pour le quartz.
- Les produits de combustion (monoxyde de carbone, oxydes d’azote et le dioxyde de soufre) sont source de risque d’intoxication aux gaz des fours (céphalées, irritations des voies respiratoires, asphyxie) : la plupart des fours industriels fonctionnent au gaz, et les gaz d’échappement des fours sont sources de dégagement éventuel de monoxyde de carbone (CO), de dioxyde de soufre (SO2), d’oxydes d’azote (NOx), soit du fait de la combustion elle-même (mauvais tirage ou réglage défectueux des bruleurs), soit du fait de la cuisson des matières.
- Toutes les fumées de métaux contenus dans la glaise peuvent entrainer des pathologies respiratoires (toux, expectoration, essoufflement), particulièrement pour certains oxydes de métaux dangereux pour la santé (nickel, chrome, cadmium...) mais aussi pour le fer et le manganèse.
Les fumées de ces oxydes métalliques sont aussi des substances allergisantes et peuvent être à l’origine de véritables asthmes professionnels. - Risques acoustiques dans les briqueteries et tuileries
Les sources de bruits sont nombreuses, créant un environnement constamment bruyant du fait en particulier des opérations d’extraction, de broyage, de criblage, moteurs et avertisseurs sonore de recul des engins, rouleaux des convoyeurs, compresseurs, vibreurs, mélangeurs, ... Les niveaux de pression acoustique engendrés par les bruits des broyeurs à leur voisinage peuvent atteindre 100 dB.
En dehors des atteintes au système auditif (déficit auditif, acouphènes...), le bruit ambiant peut entraîner une gêne ou un stress vecteur de troubles du psychisme et de pathologies qui nuisent non seulement à la santé du travailleur mais aussi à la sécurité de son travail par baisse de vigilance et de dextérité ou de concentration. - Les risques physiques dans les briqueteries et tuileries
- Les risques des manutentions
Les charges lourdes portées manuellement, ou le nombre excessif de manipulations et mouvements avec torsion du dos, rotation pour le déplacement, flexion pour le soulèvement, ou la station debout prolongée ... sont à l’origine d'accidents de travail concernent la colonne vertébrale (dorsalgies, lombosciatiques) et le vieillissement progressif des structures ostéoarticulaires des épaules, des coudes (tendinites) et des poignets : ces risques musculo- squelettiques (TMS) apparaissent en particulier lors de l’emballage, du tri à la chaîne des tuiles entraînant des gestes répétitifs.
- Les risques liés aux machines
Certaines parties des machines les opérations de nettoyage et de maintenance, les réglages, les démarrages sont sources d'accidents majeurs du fait des pièces en mouvement accessibles (par exemple les broyeurs, les cribleurs etc.), en particulier lors des mises en marche intempestives, des arrêts anormaux suite à une rupture d’énergie : coupures aux mains, lacérations des avant-bras ou écrasements lors des nettoyages par exemple.
- Les risques liés aux convoyeurs à bande
Les possibilités d’accès aux différentes zones dangereuses des convoyeurs à bande, conçus pour le transport en continu sur un itinéraire prédéterminé de plusieurs centaines de mètres, notamment au cours d’interventions de maintenance (nettoyage sous le convoyeur, déblocages, débourrages, ...) génèrent des accidents pouvant être graves, du fait des éléments mobiles ou de la courroie transporteuse et des déplacements des charges (chute du matériau transporté...).
Les dommages peuvent être dus au cisaillement et à l’écrasement entre la charge et une partie fixe ou aussi résulter de la chute de la charge ou d’un choc avec la charge. Des risques mécaniques de happement, de coincement, d’enroulement existent notamment pour les travailleurs chargés de la maintenance, avec la possibilité que des parties du corps et/ou des vêtements soient entraînés par les convoyeurs en marche au contact des organes tournants (rouleaux...).
Ces dangers sont présents par exemple lorsque les ouvriers essayent de débloquer le bourrage des mécanismes (enlèvement d’une accumulation) lors d’un incident de fonctionnement avec l’installation encore en mouvement ou démarrant inopinément.
- Les risques liés aux engins et à la circulation sur le site
Un trafic intense de poids lourds, d’engins d'extraction et/ou de chargement, de chariots de manutention est intrinsèquement dangereux, générant potentiellement des accidents graves.
Les dangers concernent non seulement les conducteurs d’engins mais également tous les ouvriers qui se trouvent à proximité, qui peuvent être heurtés par l’engin ou sa charge du fait de l’inattention, du manque de visibilité, ...
Les situations à risques tiennent aux voies de circulation (largeur et la géométrie de la voie, signalisation, assise du sol...) aux camions et engins (état des freins, pneumatiques, direction, éclairage, avertisseurs sonores ou lumineux ...), à l’organisation des flux circulatoires et aux comportements humains (précipitation, stress, indiscipline, alcool) : tous ces facteurs agissent de façon autonome mais aussi inter-dépendamment, multipliant les possibilités d’accident.
La circulation sur le site est constituée de multiples flux dont la superposition, les interférences et la confusion entre piétons, engins et autres véhicules très différents (quant à leur vitesse, gabarit, manœuvrabilité) entrainent des possibilités d’accidents de toute origine, lors des croisements, manœuvres sur les différents espaces du site.
Le danger de collision avec d’autres engins dans la même zone de travail est possible.
Le déplacement des engins sur le site peut générer des risques de heurts avec les travailleurs à pied.
Des blessures peuvent être occasionnées par les godets ou par les câbles ou les sangles d’arrimage, par la manutention lourde de patins de calage, de pièces détachées...
On note aussi des traumatismes suite à une chute lors de la descente de l’engin (entorses...), des projections en roulant de corps étrangers dans les yeux des ouvriers du fait d’un environnement particulièrement caillouteux et poussiéreux.
- Autres risques physiques
Chutes de plain pied sur sol glissant, inégal ou encombré, électrocution par contact direct ...
Pour mémoire, l'infestation par des vers parasites (ankylostomes) vivant dans le sol humide et les eaux boueuses provoquait jadis l'anémie des briquetiers due à de nombreuses petites hémorragies répétées (Tableau n° 28 RG, ankylostomose professionnelle (ou ankylostomiase), anémie engendrée par l'ankylostome duodénal).
Les mesures de prévention des risques dans les briqueteries et tuileries
Les opérations sont aujourd’hui pour une large part automatisées et mécanisées : les manutentions, le moulage, l’enfournement, le défournement... Le process des grandes briqueteries et tuileries industrielles ainsi fortement modernisé, la prévention collective résulte alors par exemple de l’utilisation de systèmes de fabrication automatisés et de dispositifs mécaniques comme l’extraction de poussières qui permettent de réduire l’exposition des travailleurs et de diminuer considérablement les risques physiques, chimiques. Le process d'une installation de fours piloté par un contrôle informatisé centralisé réduit les interventions dans les ateliers et minore ainsi beaucoup les possibilités de sources d’exposition chimique et thermique.
Toutefois, des incidents dans l’automatisation des opérations, des fuites, des dysfonctionnements des asservissements... génèrent des dangers et nécessitent également des interventions de maintenance qui restent dangereuses. Par ailleurs, dans les petites briqueteries ou tuileries dans lesquelles les volumes traités sont bien inférieurs, les pratiques sécuritaires sont beaucoup moins mises en œuvre et maîtrisées.
Les ateliers de fabrication de briques et de tuiles doivent faire l’objet d’une analyse poussée des risques pour permettre la rédaction du Document Unique de Sécurité en appréciant à la fois l’environnement matériel et technique (outils, machines, produits utilisés) et l’efficacité des moyens de protection existants et de leur utilisation selon les postes de travail.
Les analyses de risques sont confiées à des spécialistes de la sécurité au travail (hygiéniste, ingénieur sécurité). Les rapports d’intervention et de maintenance seront aussi intégrés à la documentation de sécurité au travail de l’entreprise et communiquées au médecin du travail et au CHSCT.
Les salariés doivent être aussi informés à propos des produits dangereux mis en œuvre et formés aux pratiques professionnelles sécuritaires.
La prévention la plus efficace est la prévention primaire avec la mise en place de technologies qui permettent des actions sur les produits (suppression ou emploi de produits de substitution de moindre impact potentiel sur l'homme) et/ou des actions sur les procédés (emploi de matériels ou de machines supprimant ou limitant au maximum les impacts, par de très faibles rejets atmosphériques, par de bas niveaux sonores...).
Enfin, le port d’équipement de protection individuel (combinaison, gants, chaussures et lunettes de protection, masques...) est obligatoire pour réduire le risque d’exposition non totalement éliminé par les mesures de protection collectives, ainsi que la présence d’installations et de matériel de premier secours.
- Une ventilation des lieux de travail adéquate
La ventilation et l’aération des lieux de travail jouent un rôle essentiel pour limiter la concentration de l'ensemble des vapeurs dans l'air ambiant et les évacuer des lieux de travail, de façon à respecter les valeurs limites fixées par les réglementations et éviter ainsi les conséquences sur la santé des travailleurs.
La ventilation mécanique générale, extracteur d’air pour l’aspiration des vapeurs, doit assurer un renouvellement d'air en permanence afin de limiter les risques pour la santé, en évitant l’accumulation de vapeurs nocives et explosives, par extraction et soufflage : l'air est transporté dans le local par un ventilateur de soufflage et extrait du local par un ventilateur d'évacuation. L’extraction de l'air se fait grâce à un système de collecte par ces ventilateurs et des gaines de diffusion, réseau de conduits jusqu'aux filtres et aux épurateurs dans l'installation d'air soufflé qui permettent de nettoyer l'air, puis de l’évacuer à l'extérieur par rejet dans l'atmosphère.
Les composants aérauliques comme les ventilateurs, les conduits doivent être accessibles et faciles d’entretien et de nettoyage. En particulier, les réseaux s’encrassent rapidement avec de filtres hors d’usage, une évacuation des condensats obstruée... L'entretien régulier du système de ventilation (nettoyage des conduits d'extraction, changement des filtres) est une condition indispensable de bon fonctionnement.
Ces dispositifs doivent être complétés par une ventilation avec extraction localisée des fumées et particules métalliques, ... ou sur les équipements avec filtres à manches, épurateurs ou autres collecteurs de poussières : les installations destinées à traiter les fumées des fours sont indispensables.
Pour mesurer l’efficacité des installations de ventilation, la mesure périodique des agents chimiques par prélèvements d'atmosphère et analyses des vapeurs, poussières, gaz (dont CO), est importante : contrôles réguliers et fréquents ou, mieux, contrôle permanent complété par un système d’alarme automatique.
La valeur limite correspond à sa concentration dans l’atmosphère dans laquelle une personne peut travailler pendant un temps donné sans risque d’altération pour sa santé.
La Valeur Limite d’Exposition (VLE) est la concentration maximum à laquelle un travailleur peut être exposée au plus pendant 15 mn sans altérations physiologiques : ce critère a pour but d’éviter les effets immédiats sur l’organisme.
La Valeur Limite Moyenne d’exposition (VME) est la limite d’exposition d’un travailleur pour une exposition régulière de 8h par jour et de 40h par semaine : ce critère a pour objectif d’éviter les effets à long terme sur l’organisme.
Ces valeurs limite s'expriment en "ppm" (partie par million) ou en mg par m3
La norme EN 481 concerne l’échantillonnage de poussières ou d’aérosols sur les lieux de travail et donne les caractéristiques des instruments à utiliser pour déterminer les concentrations.
Les mesures et analyses peuvent être faites par l’employeur ou par un laboratoire extérieur et le respect des valeurs limites doit être vérifié au moins annuellement.
Si la valeur limite d’exposition est dépassée, cela permet d’imposer un arrêt temporaire d'activité pour remédier à la situation, puis il faut réaliser un nouveau contrôle sans délai.
Ces rapports d’analyses métrologiques, d’intervention et de maintenance seront intégrés à la documentation de sécurité au travail de l’entreprise (Document Unique de Sécurité).
La maitrise de l’empoussièrement passe aussi par le confinement des appareils : le capotage et le bâchage des appareils enferme le lieu d’émission de la poussière et évite qu’elle se disperse dans l’air ambiant : toile sur les cribles, bâchage des convoyeurs et des camions. - L’utilisation de machines et équipements adaptés
Le process des grandes usines modernes de fabrication de briques et de tuiles est fortement mécanisé et automatisé : l’isolement des travailleurs dans des salles de contrôle ou des cabines, climatisées et insonorisées, réduit considérablement les risques thermiques, physiques (manutention, coupures...) et acoustiques.
- Protection contre les risques thermiques : bonne isolation thermique, inaccessibilité des parties chaudes des installations en installant des écrans thermiques.
- Des bacs de rétention spécifiques, pour le stockage des produits chimiques, doivent être mis en place pour recueillir les fuites et déversements accidentels. Les lieux de stockage des matériaux pulvérulents livrés en vrac doivent être fermés et isolés des autres lieux de travail (dans des conteneurs ou silos pour éviter la production de poussière).
- Employer des systèmes clos pour acheminer les matières premières sèches (convoyeurs fermés, ...).
- Des sols avec des revêtements antidérapants, un drainage satisfaisant et des caillebotis, pour éviter le dépôt de liquides : les sols doivent être de plus nettoyés régulièrement et tout produit accidentellement répandu, lors d’une fuite ou déversement, immédiatement épongé pour éviter les glissades et chutes de plain-pied.
- Dispositifs de sécurité des machines :
Toute machine doit porter les avertissements, signalisations et dispositifs d’alerte indispensables pour assurer la sécurité des travailleurs afin de supprimer ou réduire au minimum les risques de coupure, d’entraînement, d’écrasement, de cisaillement. Cette identification doit être réalisées par des pictogrammes et couleurs normalisées. Les éléments de travail doivent être disposés, protégés, commandés ou équipés de façon telle que les opérateurs ne puissent atteindre la zone dangereuse (carters de protection des organes en mouvement...).
Les panneaux de signalisation seront choisis et disposés de façon à être perçus et compris facilement sans ambiguïté.
Chaque machine doit être munie d’un ou plusieurs dispositifs d’arrêt d’urgence et en cas d'ouverture clairement identifiables, accessibles et en nombre suffisant, permettant d’éviter les situations dangereuses en train de se produire.
- Dispositifs antibruit
Les machines et équipements doivent être conçues et fabriquées de façon à ce que les émissions sonores soient réduites au niveau le plus bas possible en application d’une directive européenne 2003/10/CE du 6 février 2003 concernant les prescriptions minimales de sécurité et de santé relatives à l'exposition des travailleurs aux risques dus aux agents physiques liés au bruit.
Par le choix ou l’achat de machines et par l’utilisation de procédés silencieux, les émissions sonores peuvent être maintenues à un bas niveau (par exemple, vibreurs insonorisés).
Les machines bruyantes doivent être munies de capots insonorisants et pour réduire les bruits transmis par les sols et les structures, des blocs anti-vibrations peuvent être placés entre la machine et la surface d’appui.
En ce qui concerne les locaux, les réflexions sur les murs entraînent une augmentation du niveau sonore dans le local et des mesures préventives de correction acoustique comme la mise en place d’un plafond ou faux-plafond absorbant, de cloisons amovibles recouvertes de produit anti-réverbérant à proximité des installations, réduisent à la fois le niveau sonore et protègent les postes de travail avoisinants.
- Aménagement d’équipements et de plans de travail ergonomiques, selon le type de poste occupé : sièges adaptés aux opérations (par exemple assis debout), apparaux de levage (palans pour soulever les charges lourdes, potences...), bandes transporteuses, tables adaptées et réglables, bonne hauteur et profondeur des plans de travail,
- Installations électriques conformes aux normes de sécurité : mise à la terre appropriée de l'équipement pour dissiper et diriger à la terre en toute sécurité les charges électriques accumulées, protection contre les contacts avec les masses mises accidentellement sous tension par un dispositif de coupure automatique en cas de défaut d’isolement et utilisation de disjoncteurs différentiels 30 mA de grande sensibilité...
- Entretien et vérification des bruleurs, des cheminées....
Le respect des recommandations des constructeurs et un entretien régulier des installations sont des éléments essentiels pour limiter les risques accidentels et pour prévenir des émanations.
Ainsi, l’utilisation et l'entretien des machines doivent être effectués par un personnel qualifié, spécifiquement formé.
Des machines utilisées de manière non conforme ou mal entretenues et non vérifiées périodiquement créent un risque chimique supplémentaire. - Des conditions de circulation adéquates
Des règles de circulation adéquates sont indispensables pour diminuer les risques liés à la circulation des engins : il faut prendre une série de mesures préventives, ayant trait à la prévention organisationnelle (plan de circulation, règles et procédures...), technique (aménagement des voies, entretien des engins, signalétique...).
- L’établissement d’un plan de circulation permet de déterminer le tracé des trajets effectués et leurs itinéraires et de lister les moyens de transport des matériaux et de déplacement des personnes : définir pour chaque type de véhicule les lieux de circulation et les voies autorisées, réglementer les accès à certaines zones...
Cela permet d’identifier les zones critiques des circulations (croisements multiples, ...), de prévoir des voies de décélération, d’accélération et ronds points giratoire, les zones de stationnement, l’emplacement des aires de chargement/déchargement, les zones interdites ou réservées à certains véhicules etc.
Le plan de circulation est à la fois un outil technique qui permet une vision globale de la circulation dans l’entreprise, mais aussi un outil d’information auprès du personnel, des entreprises extérieures amenées à intervenir à l’intérieur de l’entreprise (sous-traitants, maintenance ...). Ce plan doit être affiché à l'entrée.
- Séparation des flux de circulation
La limitation du nombre de collisions passe par la diminution de leur probabilité : séparation (infrastructure et marquage) entre piétons et véhicules par des cheminements dédiés pour les différents moyens de transport, passages piétons spécialement aménagés et protégés (chaines, rambardes de sécurité, enrochements...).
En règle générale, il convient de dissocier les voies et les usages (aménagement des espaces de bâchage distincts des quais de chargement par exemple).
- L’entretien des pistes
Des pistes mal entretenues entraînent des secousses et des heurts (ornières...), une émission de poussières excessive :
- réglementation de la vitesse des engins et la surveillance de son respect permet de limiter les envols de poussières tout en réduisant les risques d’accidents de la circulation,
- nettoyage et l’entretien des pistes et des voies d’accès avec un revêtement au sol à la résistance adaptée aux sollicitations, sans trous, non dérapant, par l’enrobage des voies permanentes, le recouvrement des pistes par des graviers pour drainer les eaux et éviter la formation de boues.
- La signalétique de circulation
Des pictogrammes de signalisation ou panneaux permettent d’aménager des cheminements sécurisés en attirant l'attention ou en signalant un danger spécifique à certains endroits (repérage des obstacles, ...). L’efficacité de la signalisation dépend de son emplacement et doit être visible soit à l’accès à une zone pour un risque général, soit à proximité immédiate d’un risque déterminé ou d’un objet (poteau, tuyauterie...) à signaler. Une signalétique redondante ou excessive est à proscrire (Ex : nombre excessif de panneaux à proximité immédiate les uns des autres, signal lumineux à proximité d'une autre émission lumineuse,....).
- Ergonomie des engins
- Sécurisation de l'accès et de la cabine : marchepied antidérapant et échelle d'accès complétée par des poignées ou des mains courantes.
- Cabine insonorisée et climatisée.
- Poste de conduite ergonomique avec siège adapté.
- Entretien régulier de l'engin : les engins doivent faire l’objet de vérifications annuelles consignées sur le registre de sécurité. La présence et le bon fonctionnement des équipements de sécurité des véhicules et engins est indispensable : éclairage, avertisseur sonore et/ou lumineux de recul, freins, pneumatiques, direction, moyens de calage, rétroviseurs. - Dispositifs de protection et de sécurité des convoyeurs à bande
Il s’agit d’établir une distance de sécurité vise à empêcher un travailleur de toucher les éléments du convoyeur qui représentent un danger, en installant des protecteurs fixes de maintien à distance, d’angle rentrant, enveloppant les rouleaux ou les poulies et courroies, munis d’inter-verrouillage...
Les procédures de consignation doivent être respectées pour les travaux de maintenance, particulièrement pour ces installations de très grande longueur : sinon, de nombreux accidents surviennent suite à une mise en fonctionnement alors qu’une intervention est en cours. Il s’agit d’éviter une mise en route intempestive du convoyeur. Tout organe qui permet la séparation du convoyeur de sa source d'énergie doit être immobilisé en position de sécurité par mise en place de verrouillage physique (cadenassage...). La condamnation doit toujours être signalée par affichage pour information claire et permanente de la réalisation de la condamnation (étiquettes de consignation...) - Le respect des règles d’hygiène
Une bonne tenue des sols des locaux par aspiration ou par un procédé à l’humide (jet d’eau ou système eau/vapeur), est essentielle pour éviter l’accumulation de déversements et de poussières sous ou autour des machines. Les déversements peuvent créer un danger de glissement et par conséquent doivent être nettoyés immédiatement.
Des mesures complémentaires d’hygiène des locaux doivent être mises en œuvre tel le nettoyage régulier des machines et des parois de l’atelier à l’aide d’un aspirateur industriel adapté avec un filtre absolu de haute efficacité pour les particules (HEPA) qui ne disperse pas les poussières dans l’air (pas de soufflette à l’air comprimé, ni balayage).
Des lavabos, postes de rinçage oculaire et des douches de sécurité doivent se trouver à proximité des postes de travail. Celles-ci permettent les mesures d'hygiène générale : lavage des mains fréquent avec moyens adaptés, douche en fin de poste... En effet, le respect des règles d’hygiène s’étend aux comportements individuels : ne pas avoir les mains sales afin de ne pas ingérer par inadvertance un produit toxique et ne pas manger sur le lieu de travail.
Le personnel doit avoir à sa disposition des vestiaires et des sanitaires correctement équipés et en nombre suffisant. Des vestiaires doubles doivent être mis à la disposition des travailleurs : l’entreposage des tenues de travail doit avoir lieu à l’abri de la poussière et des souillures (le rangement des tenues de ville et des tenues de travail doit être séparé).
Des procédures de travail en ambiance chaude doivent être édictées et respectées de manière à réduire la contrainte thermique : absorption en quantité suffisante d’eau et de boissons renfermant des sels minéraux, rythme travail-repos aménagés en zone tempérée. - Le port d’équipements de protection individuel adéquat
Les équipements de protection individuelle sont nécessaires pour réduire le risque d’exposition non totalement éliminé par les mesures de protection collectives précédentes : gants, casque, vêtements de protection, chaussures et lunettes de sécurité, différents et adaptés à la tâche effectuée.
La fourniture d’un équipement de protection individuelle est particulièrement nécessaire aux opérateurs travaillant dans des lieux poussiéreux ou près des fours.
S’il y a possibilité de contact avec la main lors des transvasements de produits chimiques par exemple, il s’avère indispensable de porter des gants de protection adaptés au produit manipulé : il n'existe pas de gant de protection universel. Le type de gants conseillé, imperméables, à longues manchettes, pour éviter la pénétration des produits à l’intérieur, doit être adapté aux différents produits manipulés selon leur composition qui figure sur la Fiche de Sécurité (FDS). Des gants appropriés doivent être aussi utilisés pour éviter les coupures aux mains, d’autres pour la protection contre la chaleur ainsi que des manchettes en isolant thermique, pour les pièces à la sortie des fours.
Des vêtements de protection contre la chaleur, tablier, lunettes de sécurité avec verres filtrant les infrarouges complètent la protection pour les travailleurs exposés à la chaleur.
En cas d’urgence ou pour des travaux exceptionnels d’entretien de courte durée, si les systèmes de ventilation ou d’aspiration ne suffisent pas à empêcher l’accumulation de poussières, un appareil de protection respiratoire adéquat doit être fourni pour éviter l’exposition à une concentration élevée : masque anti-poussière FFP2 ou à cartouche FFP3 avec un filtre adapté (cas pour la réfection des fours), selon le niveau de l’empoussièrement.
De même, des protections auditives peuvent être recommandées pour compléter les mesures collectives qui s’avéreraient insuffisamment efficaces.
Des postes de rinçage oculaire et les douches de sécurité doivent se trouver à proximité des postes de travail pour ôter les projections de poussières ou autres corps étrangers dans les yeux. - La surveillance médicale
Pour les briquetiers et tuiliers exposés aux poussières de silice et de métaux lourds, au bruit, et travaillant de nuit, il faut réaliser des visites médicales régulières dans le cadre d’une surveillance médicale renforcée.
- Tests respiratoires (spiromètre) à l’embauche pour détecter une déficience des fonctions pulmonaires et tous les 2 ans pour dépister l’apparition des troubles respiratoires.
- Radiographie thoracique si nécessaire, épreuves fonctionnelles respiratoires (EFR) conseillées - La formation et l’information du personnel
La formation, par un organisme agréé, sur les dangers des produits utilisés et sur les moyens de se protéger, est indispensable : par exemple, comprendre les étiquettes du contenant des produits, informer sur le risque potentiel de maladies pulmonaires et sur les moyens de les prévenir, connaître l’attitude à adopter en cas de fuite ou de déversement accidentel ou d’émissions accidentelles de gaz, savoir utiliser les E.P.I adéquats, formation aux premiers secours et incendie, formation PRAP (Prévention des Risques liés à l'Activité Physique) ...
Plus particulièrement, pour la conduite d’engins :
Les mesures de formation relative à l’utilisation des équipements de travail mobiles automoteurs (Code du Travail R.223-13-19) imposent une obligation de formation au personnel susceptible de les conduire et une aptitude médicale. Le Code du travail fait obligation de délivrer une autorisation de conduite au personnel pour tous les engins de chantier mobiles à conducteur porté : en effet, le chef d’établissement doit se conformer aux obligations en matière de contrôle de connaissances et savoir-faire du conducteur pour la conduite en sécurité (art R 233-13-19).
La délivrance d’autorisation de conduite est conditionnée par la réussite au test d’évaluation, sanctionnée par le Certificat d’Aptitude à la Conduite En Sécurité (CACES). Ces contrôles sont réalisés par des testeurs qui appartiennent à des organismes agrées ; la qualification de ces organismes et le contrôle de leurs prestations sont confiés à des organismes conventionnés par la CNAMTS et accrédités par le COFRAC.
L'activité de conducteur d’engins nécessite une formation spécifique pour chaque type de machine et c’est pourquoi il existe différents types de CACES.
Des stages de perfectionnement à la conduite permettent de maintenir les aptitudes à bon niveau.
Juillet 2015
Partagez et diffusez ce dossier
Laissez un commentaire
Votre adresse de messagerie ne sera pas publiée.