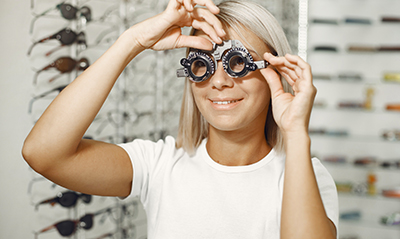
- Accueil
- Formation Conseils
- Fiches Métier
- La prévention des risques de la robotisation industrielle
La multiplication des robots industriels et leur adaptation très rapide à un grand nombre de tâches manufacturières ou logistiques expose les travailleurs à des risques pour leur sécurité : ceci est d'autant plus accentué dans les cas des nouveaux robots collaboratifs qui partagent un même espace de travail, en réalisant des travaux avec les opérateurs...
La multiplication des robots industriels et leur adaptation très rapide à un grand nombre de tâches manufacturières ou logistiques exposent les travailleurs à des risques pour leur sécurité : ceci est d'autant plus accentué dans les cas des nouveaux robots collaboratifs qui partagent un même espace de travail, en réalisant des travaux avec les opérateurs. Les dangers peuvent survenir lors de l'utilisation du robot mais aussi lors de sa maintenance ou de son réglage : risques mécaniques élevés de collision avec l'utilisateur, du fait notamment de la vitesse élevée d'exécution, du manque ou de la difficulté d'anticipation de certains mouvements des parties mobiles, de la force des impacts … , risques psychologiques liés à l'interaction homme-machine (sentiments de dépendance, de perte d'autonomie et d'identité, excès de charge mentale …).
La sécurité de l'homme dans les solutions robotisées passe par des dispositifs de protection et de signalisation matérielle et des barrières physiques pour les robots industriels « classiques », mais la sécurité des opérateurs pose des problèmes nouveaux pour les robots collaboratifs pour lesquels doivent être mises en œuvre des solutions de sécurité " immatérielle ", dans un espace ni délimité ni protégé, avec des techniques logicielles de vision et/ou de détection de collision à base de capteurs de contact et d'effort.
Des normes techniques relatives à la robotique industrielle encadrent la relation homme-machine.
Les principaux risques de la robotisation industrielle
Le robot industriel est une structure mécanique dotée d'un bras manipulateur programmable généralement avec six degrés de liberté, trois axes destinés au positionnement et trois axes pour l'orientation, permettant de déplacer et manipuler un outil effecteur dans un espace de travail donné et contrôlé par des capteurs divers. Certains robots utilisent comme énergie de fonctionnement des moteurs électriques, d'autres utilisent aussi des vérins hydrauliques.
La programmation des mouvements et des séquences d'un robot industriel sont réalisées au moyen d'un microordinateur industriel ou automate programmable doté du logiciel adéquat.
Les robots industriels sont le plus souvent affectés à des opérations spécifiques (soudure, peinture, découpe, assemblage, manutention, conditionnement …) en exécutant des consignes assez simples à un poste fixe, mais, grâce aux progrès de l'intelligence artificielle, des capteurs et de la mécatronique, on voit apparaître de plus en plus des robots dotés d'une vision et de possibilités d'apprentissage, de mobilité et d'autonomie.
Les robots industriels améliorent considérablement la productivité en réduisant drastiquement les coûts de main d'œuvre et sont de plus en plus utilisés dans l'industrie et la logistique dans les travaux routiniers et dangereux et participent aussi de la sorte à améliorer les conditions de travail dans les ambiances de charge physique importante ou répétitive, de nuisances sonores, chimiques, radiologiques, biologiques : en effet, les robots industriels « classiques », durant leur phase opérationnelle, fonctionnent normalement hors la présence du personnel, qui se trouve ainsi éloigné du process et à l'abri des risques qui lui sont inhérents.
Toutefois, si une présence humaine inopportune peut néanmoins survenir, cette présence est de toute façon indispensable lors des opérations d'installation, de réglage, de formation et d'entretien : le travailleur peut alors être en relation naturelle ou accidentelle avec les parties mobiles du robot ou de son alimentation électrique ou hydraulique et de leurs dangers.
Quant aux nouveaux robots collaboratifs aux postes de travail les plus dangereux ou les plus pénibles (service professionnel, assistance physique …), ils représentent à la fois une grande opportunité d'améliorer la compétitivité et un effet bénéfique global sur la santé du travail, mais également des risques pour la sécurité des travailleurs qui interagissent avec ces machines. Les utilisations nouvelles des robots industriels collaboratifs, comme l'aide ou l'assistance à la manipulation de charge, permettront de les sortir des usines et de travailler sur les chantiers du BTP par exemple.
- Les différentes causes des risques des robots industriels
La vitesse de déplacement du robot et la difficulté d'anticiper certains mouvements de ses parties mobiles, la mise en œuvre d'une énergie considérable, sont des facteurs de risque physique important.
De plus, en cas d'association homme-robot, les conditions de travail peuvent être particulièrement éprouvantes du fait des performances excessives du robot en cadence et régularité du travail si les interfaces homme-machine et machine-homme manquent d'ergonomie robotique.
En fonctionnement opérationnel,
- la pénétration par négligence, distraction ou nécessité dans la zone d'évolution du robot, la neutralisation des protections, représente un danger majeur : même après un arrêt d'urgence, le robot peut rester dangereux du fait de son énergie résiduelle non purgée de ses composants électriques ou hydrauliques, d'un mouvement imprévu du bras.
- Le dysfonctionnement du système robotisé lui-même peut avoir différentes origines : défaillances ou pannes ou modifications hasardeuses des moyens de protection, défaillances du système électronique de commande, du logiciel …
- Le risque peut avoir une origine conceptuelle comme la mauvaise disposition des protecteurs ou la mauvaise réaction à une situation anormale.
En installation, réglage ou maintenance, les risques sont augmentés lors des essais fonctionnels ou des réparations : en effet, le personnel est alors amené à pénétrer dans la zone de travail du robot et à le faire fonctionner, est amené à effectuer des interventions qui ne sont pas toujours répétitives et par suite, soumises à de nombreux aléas ou situations inhabituelles, exposant au contact avec des pièces nues sous tension ou fluides sous pression, avec une pression temporelle forte, surtout si la machine en cause est vitale pour la production, avec une lourde charge mentale pour des systèmes industriels automatisés qui deviennent plus complexes et donc plus difficiles à maintenir en état. La majorité des accidents en milieu industriel robotisé se produisent lors des interventions de mise au point, de démarrage et de maintenance des systèmes. - Les différents risques des robots industriels
La collision avec le robot lors du mouvement, avec son bras ou une pièce en cours de manipulation ou un outil solidaire du bras, peut engendrer de sérieuses blessures accentuées par l'énergie cinétique élevée et/ou par le caractère contondant ou tranchant de l'outil : trois critères de blessures "force d'impact", "force de coincement/d'écrasement" et "pression/ pression superficielle" déterminent la profondeur de pénétration de la peau et des tissus sous-jacents accompagnée de plaies saignantes, de fractures ou autres lésions du système musculo-squelettique.
Comme avec les autres machines-outils ou engins, les risques de happement des membres, des vêtements ou des cheveux, d'écrasement ou de coincement avec un obstacle fixe, de projection d'objet ou d'éjection de matériaux, d'émissions sonores excessives, sont d'autres risques physiques des robots.
D'autres risques physiques ne sont pas spécifiques aux ateliers robotisés, mais communs à toute activité industrielle : chutes de plain pied sur sol glissant, inégal ou encombré, électrisation/électrocution par utilisation d'outillage défectueux ou contact avec des pièces nues sous tension …
Plus difficiles à appréhender, les risques psychologiques, notamment avec l'usage de robots collaboratifs, sont encore peu connus par manque de recul et d'études, et il existe des lacunes entre les progrès réalisés dans l'application de la robotique industrielle et son large et croissante diffusion dans toutes les industries et la connaissance de leur impact sur la santé psychique et l'augmentation du stress au travail :
- les réponses organisationnelles à toutes les exigences de productivité entrainées par la robotisation qui s'étendent au personnel amené à travailler avec les robots, se caractérisent par une grande augmentation des pressions de toute nature sur les délais, la quantité, la qualité de la production.
- L'intensification de la charge mentale due aux nouvelles technologies informatiques ou d'automatisation est facteur de risque psychologique.
- L'isolement au sein d'équipes clairsemées et de vastes usines quasi-vides de présence humaine, la réduction d'autonomie, la perte d'identité face à des robots sont des conséquences possibles de la robotisation : interaction constante entre le travailleur et le robot, peu de communication avec son entourage, perte d'initiative ou marge de manœuvre dans les opérations, les cadences et la précision, dépendance à la machine ressentie comme excessive.
- Anxiété liée à l'évitement et à l'appréhension des contacts répétés avec le robot.
La sécurité des robots industriels
Les dispositifs techniques et les conditions de sécurité nécessaires à l'utilisation des robots industriels sont un des éléments fondamentaux au développement de l'automatisation des industries manufacturières dans les pays développés, atout pour stopper ou freiner les délocalisations, voire susciter des relocalisations : cet impératif de sécurité, déjà prégnant dans le cas des robots « classiques » , l'est d'autant plus dans le cas du travail collaboratif sans barrière, ni sécurité matérielle entre l'homme et robot ; la robotique collaborative constitue à la fois une évolution émergente majeure de la robotique industrielle et une extension des champs d'application de la robotique à l'assistance au geste dans de nombreuses activités professionnelles. La robotique collaborative est une opportunité de retrouver une compétitivité industrielle et il est donc essentiel que tous les aspects sécuritaires soient correctement pris en compte dès la conception, lors de l'intégration et de l'utilisation des robots, ainsi que la problématique de la place de l'homme dans les solutions robotisées.
C'est pourquoi la sécurité des robots industriels est régie par des normes très strictes (ISO 10218).
- Les mesures préventives en robotique « classique »
Protéger l'utilisateur du danger potentiel du robot en mouvement nécessite de créer une zone protégée par une enceinte de protection avec un accès restreint et de former aux risques et aux consignes de sécurité des systèmes robotisés. Lors du fonctionnement normal du robot, il convient donc d'interdire, au moyen de protecteurs, la présence humaine dans la zone de travail maximale du robot, y compris la zone occupée par la pièce usinée : par exemple, isolement par une cage en polycarbonate ou un grillage, accès protégé par des barrières inter- verrouillées avec le fonctionnement du robot, zones de coincement éliminées en respectant un dégagement suffisant par l'utilisation de cages munies de portes de sécurité. Des systèmes photoélectriques de détection de présence, des systèmes de vision, des capteurs de contact, viennent compléter les dispositifs en sécurité en interrompant et/ou déviant le mouvement du robot.
Lors de la mise au point ou de la maintenance du robot, la vitesse d'évolution est alors automatiquement limitée, par pulsion ou par commande à action maintenue ou cycle par cycle, pour permettre à l'utilisateur d'anticiper les mouvements du robot afin de pouvoir éviter toute collision, avec une console de commande extérieure rendue inopérante. La présence d'une personne supplémentaire ayant la possibilité de couper l'alimentation de puissance du robot en cas de risques pour l'opérateur complète les mesures de prévention. - Les mesures préventives en robotique collaborative
L'offre robotique développée par les progrès de l'intelligence artificielle (capacité et rapidité de calcul et apprentissage), de la communication, et de la mobilité mécatronique, sort les robots de leur cage et les fait évoluer à proximité de leur utilisateur, imposant des solutions de sécurité plus " immatérielle ", basée sur des logiciels, des capteurs, et une sécurité fonctionnelle des systèmes de commande électriques et électroniques programmables :
l'objectif est d'anticiper, d'éviter les collisions ou d'en réduire les effets. Un élément essentiel de ces robots collaboratifs (ou collaborant) est donc de surveiller de manière ciblée et sure tous les mouvements du robot afin de le stopper ou le dévier immédiatement si la vitesse ou la force exercée sont trop élevées. Il s'agit d'avoir à la fois un robot multitâche et qui n'ait plus aucun protecteur fixe tout en étant sûr.
Pour intégrer correctement la sécurité des robots collaboratifs, il faut fixer les paramètres de fonctionnement et de contrôle sécuritaire et ergonomique : vitesse maximale de collaboration, limite de puissance de force, surveillance de la distance de sécurité avec l'opérateur avec garantie de détection et de temps de réaction, gestion des événements imprévus … Ce qui nécessite des capteurs électroniques mesurant les distances, les efforts, … et un automate programmable et un logiciel dédié prenant en compte ces éléments et transmettant ses instructions à des organes effecteurs électriques et mécaniques. - Les normes techniques relatives à la robotique industrielle
Afin d'encadrer la coopération homme-machine, notamment au plan de la sécurité des opérateurs, il existe la norme ISO 10218 (août 2011), qui spécifie les exigences en matière de sécurité, d'ergonomie, de performance des « robots pour environnements industriels ». Cette norme comporte deux parties : la première concerne les exigences de sécurité et les recommandations aux concepteurs des robots tandis que la seconde traite de la sécurité en matière d'intégration et d'utilisation des systèmes robotiques.
Novembre 2015
Partagez et diffusez ce dossier
Laissez un commentaire
Votre adresse de messagerie ne sera pas publiée.
Ces dossiers pourraient vous intéresser
Identification HSE
Créer mon compteNos rubriques
- Livres et édition
- Fiches Métier
- Materiel pédagogique
- Conseils
- Réparation matériels ATEX
- Travail en hauteur
- Sauveteur Secouriste du Travail (SST)
- Risque chimique
- Sécurité BTP
- Habilitations électriques
- Port des EPI
- Incendie - Explosion
- Gestes et postures - PRAP
- Conduite d'engins
- Prévention routière
- Formation continue à la sécurité
- Formation initiale à la sécurité
- Experts agréés auprés des CSSCT
- Formation de la CSSCT