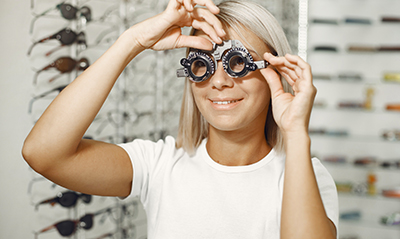
- Accueil
- Formation Conseils
- Fiches Métier
- La prévention des risques professionnels de l'impression tridimensionnelle (3D)
L’impression tridimensionnelle (3D) d’une pièce est la fabrication additive par couches successives de matériaux thermoplastiques liquéfiés pilotée par un logiciel. La forte croissance de l'impression tridimensionnelle (3D) dans de nombreux secteurs génère des risques professionnels spécifiques eux-mêmes en augmentation...
L’impression tridimensionnelle (3D) d’une pièce est la fabrication additive par couches successives de matériaux thermoplastiques liquéfiés pilotée par un logiciel.
La forte croissance de l'impression tridimensionnelle (3D) dans de nombreux secteurs génère des risques professionnels spécifiques eux-mêmes en augmentation :
- Risques chimiques : émissions de particules fines, de composés organiques volatils,
de gaz nocifs liés aux imprimantes 3D et à leurs différentes technologies.
- Risques de brulures, de chocs électriques et d’incendie : la fonte du plastique
au moyen de la chaleur ou d’un laser exige beaucoup de chaleur et d’énergie électrique.
- Risques physiques de l’ébavurage, ponçage, sablage... dans les post-traitements
éventuels des produits et troubles musculo-squelettiques associés à une mauvaise
ergonomie du poste de travail.
Ces risques chimiques, thermiques, électriques, physiques de l’utilisation des imprimantes 3D dans les « fab labs » (ou « ateliers de fabrication numérique ») peuvent être maîtrisés par l’utilisation de machines et d’équipements et la présence d’une installation électrique et de protection incendie conformes aux normes, la captation de gaz et de poussières au plus près de leur point d’émission, une ventilation efficace, et par le respect des exigences essentielles de sécurité (hygiène des locaux...), de protection individuelle et de formation des opérateurs.
Les principaux risques de l’impression 3D
- Généralités sur les imprimantes 3D
Des produits fabriqués par des méthodes telles que l'estampage de métal ou l'injection dans des moules peuvent désormais être obtenus par le dépôt de couches successives de matière plastique en fusion par impression tridimensionnelle piloté par un logiciel : destinés à de faibles volumes, l’impression 3D réduit significativement les temps et coûts de développement des prototypes ou de fabrication de pièces de rechange, permet un contrôle très précis du matériau travaillé et permet de créer des composants aux structures internes complexes en une seule impression, dans la construction mécanique ou aéronautique, dans le secteur médical (prothèses ...), dans l'industrie des loisirs, ...
L’impression tridimensionnelle s’appuie sur plusieurs types de technologies, mais basées toutes sur la découpe numérique d’un objet virtuel 3D en lamelles 2D de très fine épaisseur, ensuite déposées physiquement une à une par l’imprimante en les fixant sur les précédentes, pour obtenir l'objet réel étape par étape : la production additive, par couches successives, génère de petites quantités de matériaux jusqu’à l’obtention d’un produit en trois dimensions, numérisé en couches dans un fichier CAO (Conception Assistée par Ordinateur).
Les technologies les plus utilisées sont :
- la FDM (Fused Deposition Modeling), modelage par dépôt de matière
thermoplastique en fusion, utilise principalement le PLA (acide polylactique)
et l’ABS (acrylonitrile-butadiène-styrène) : le principe consiste à superposer,
par extrusion dans une buse, des couches du matériau thermoplastique
préalablement fondu à partir d’un filament enroulé sur une bobine.
Une fois déposé, le matériau fusionne avec la couche précédente et se solidifie
en se refroidissant. Les températures d’extrusion vont de 180 à 260 °C,
et la température du plateau chauffé qui supporte l’objet fabriqué peut atteindre
90 à 110 °C.
- la stéréolithographie utilise de la résine époxy liquide et un laser
avec lumière UV : les molécules se durcissent sous l’effet de la lumière
ultraviolette par photopolymérisation tout en se liant aux couches adjacentes
et ceci couche après couche.
- le SLS (Selective Laser Sintering), frittage sélectif par laser, utilise une poudre
de polyamide, de polyuréthane, polystyrène, nylon ... ou de certains métaux
et un rayon laser avec lumière infrarouge qui assemble la poudre pour créer
la forme souhaitée au lieu de l’impact.
Il y a différentes sortes de risques dans l’impression 3D, liés aux produits, aux procédés et aux machines utilisées : - Les risques chimiques de l’impression 3D
Lors de la transformation des matières plastiques et de la polymérisation, l’élévation de la température peut entraîner la libération de poussières, de nanoparticules, de gaz et de produits volatils potentiellement dangereux. L’impression 3D utilise différentes matières plastiques et résines avec libération possible de monomères des filaments thermoplastiques polymères ou de produits de base résiduels, mais utilise aussi des solvants et peintures dans la finition des pièces. Des produits de décomposition thermique (émanations et / ou vapeurs) peuvent ainsi être émis pendant les opérations d’impression et de finissage.
Par exemple :
- les filaments en nylon ... rejettent dans l’air environnant du caprolactame irritant et toxique par inhalation, ou par absorption à travers la peau et classé comme « probablement non-cancérigène pour l’homme » par l’Organisation Mondiale de la Santé.
- les filaments de type ABS rejette du styrène dans l’atmosphère, classé comme cancérigène par l’Agence Internationale de Recherche sur le Cancer.
- les processus de fusion laser avec des poudres métalliques ultrafines présentent un risque respiratoire quand elles sont en suspension dans l’air.
L’exposition fréquente et prolongée des opérateurs des imprimantes tridimensionnelles à ces poussières et composés gazeux irritants et/ou sensibilisants, à des vapeurs de solvants, génère des risques de réactions allergiques, de troubles respiratoires par inflammation de la muqueuse nasale et bronchique, d’irritation des muqueuses oculaires, de troubles neurologiques pour certains d’entre eux (styrène).
Les matières plastiques sont aussi une cause fréquente de dermatoses professionnelles avec des composants irritants et allergènes (monomères et certains additifs).
Les solvants et le styrène affectent des organes cibles divers : irritations de la peau, des yeux et de la gorge, lésions des organes et presque tous les solvants organiques provoquent des troubles digestifs du système nerveux, des maux de tête, des vertiges. Par leur action liposoluble, tous les solvants peuvent provoquer une dessiccation cutanée avec risque de dermatites pour des contacts avec la peau répétés et prolongés.
Les résines en poussières libérées par des opérations de ponçage peuvent être responsables de réactions d'irritation, de sensibilisation et d'allergie de la peau avec eczéma de contact touchant les doigts, les mains, les poignets et les avant-bras mais aussi le visage avec œdème des paupières par projection de particules.
La dermatite de contact allergique aux résines apparaît suite à la sensibilisation progressive à ces produits de façon spécifique du fait de la multiplicité des contacts cutanés non protégés. - Les risques thermiques des imprimantes 3D
Toutes les imprimantes FDM utilisent un important apport de calories par chauffage, provoquant des températures d’extrusion des buses qui s’échelonnent de 150° à 300°C environ pour permettre la dépose d’une couche. Mais, le matériau subit en sortie de buse un choc thermique important au contact avec le plateau qui peut occasionner des déformations des pièces par un phénomène de décollement des bords (warping) : pour éviter cet inconvénient, le plateau doit lui-même être chauffé pendant l’impression à une température de l’ordre de 100°C.
Du fait de ces procédés, les abords des imprimantes 3D sont donc exposés aux températures élevées et aux risques de brûlures thermiques.
La proximité d’une source de chaleur peut entrainer des céphalées, hypersudation, tachycardie, hypotension et, conjuguée à des températures de l’air élevée, provoquer des malaises dus à la déshydratation et des troubles circulatoires.
Les brulures peuvent notamment survenir lors du contact avec les buses et les plateaux pendant les périodes de montage, réglage et maintenance sans précaution, car la température descend lentement après une impression.
Les brulures peuvent aussi être provoquées par des surpressions occasionnant des projections chaudes de matière plastique par les orifices d’alimentation et des buses. - Les risques d’incendies et explosions
Les ateliers « fab labs » sont confrontés à un risque potentiel d’inflammation des solvants et d’explosion des poussières de matières plastiques ou des poudres métalliques (titane ...) due aux décharges électrostatiques, avec des sources de chaleur nombreuses provoquant de redoutables incendies à la mesure de la quantité de matières plastiques inflammables présentes dans l’atelier, dont la combustion dégage des gaz et fumées très toxiques.
Les risques d’incendie-explosion sont présents dans le cas de concentrations de styrène dans l’air atteignant les limites d’explosivité. Le stockage des résines dans des sacs endommagés dans des espaces clos et mal ventilés peut provoquer l’accumulation de vapeurs inflammables.
La montée en température incontrôlée de la buse suite à une défaillance de la thermistance peut causer un détachement de la buse et un départ d'incendie, de même que les courts-circuits électriques d’une installation défectueuse.
Les mesures préventives des risques de l’impression 3D
Principalement dédiées aux petites séries, les pièces imprimées en 3D sont élaborées dans des ateliers dans lesquels les pratiques sécuritaires doivent être bien mises en œuvre et maîtrisées, notamment lors des incidents dans les opérations, les fuites, ... qui nécessitent des interventions de maintenance qui restent dangereuses. Dans un cadre professionnel, le site d’implantation d’une imprimante 3D fait partie des « locaux à pollution spécifique » définis par le Code du Travail (article R4222-3), ou il est requis de respecter les valeurs limites admissibles de concentration de poussières, gaz, aérosols, ou vapeurs pour préserver la santé et la sécurité des travailleurs.
Les ateliers des fabrications en impression tridimensionnelle doivent faire l’objet d’une analyse poussée des risques pour permettre la rédaction du Document Unique de Sécurité (Décret du 5 novembre 2001) en appréciant à la fois l’environnement matériel et technique (outils, machines, produits utilisés) et l’efficacité des moyens de protection existants et de leur utilisation selon les postes de travail.
Les analyses de risques sont confiées à des spécialistes de la sécurité au travail (hygiéniste, ingénieur sécurité). Les rapports d’intervention et de maintenance seront aussi intégrés à la documentation de sécurité au travail de l’entreprise et communiquées au médecin du travail et au CHSCT.
La prévention la plus efficace est la prévention primaire avec la mise en place de technologies qui permettent des actions sur les produits (suppression ou emploi de produits de substitution de moindre impact potentiel sur l'homme) et/ou des actions sur les procédés (emploi de matériels ou de machines supprimant ou limitant au maximum les impacts, par de très faibles rejets atmosphériques, par de bas niveaux sonores...).
Les moyens de prévention à mettre en œuvre pour pallier les risques professionnels dans les « fab labs » résident ensuite dans la prévention collective (ventilation efficace de l’atelier et aspiration à la source des poussières et fumées, stockage des produits chimiques et installation électrique et de protection incendie conformes aux normes, respect des règles générales d’hygiène...) qui diminue fortement les expositions et la fréquence ces accidents, puis dans la prévention individuelle (équipements de protection) qui en diminue nettement la gravité, enfin dans la l’information et la formation à la sécurité des travailleurs.
Les salariés doivent être ainsi informés à propos des produits dangereux utilisés et formés aux pratiques professionnelles sécuritaires.
- La suppression / substitution des produits les plus toxiques
Certains choix doivent s’imposer quand c’est techniquement et économiquement possible :
- choisir des filaments émettant le moins possible de Composés Organiques Volatils et de Particules Ultra Fines, en fonction des imprimantes.
- bien utiliser les filaments dans les plages de préconisations de température de mise en œuvre du fournisseur, afin de limiter l’émission de vapeurs, en particulier pour les impressions à vitesse élevée, qui nécessitent d’augmenter la température d’extrusion du matériau. - Une ventilation des lieux de travail adéquate
Les émanations chimiques des imprimantes 3D doivent répondre aux normes des valeurs limites d’exposition professionnelle.
La ventilation et l’aération des lieux de travail jouent un rôle essentiel pour limiter la concentration de l'ensemble des toxiques dans l'air ambiant et les évacuer des lieux de travail, de façon à respecter ces valeurs limites et éviter ainsi les conséquences sur la santé des travailleurs. Une ventilation et un appoint d’air appropriés sont aussi indispensables pour empêcher l’accumulation de mélanges inflammables dans l’air.
Les installations utilisées doivent faire l’objet d’une analyse de risques et de relevés métrologiques périodiques : surveillance régulière de l'atmosphère, pour vérifier l'efficacité des mesures d'aspiration par dosages atmosphériques.
La ventilation mécanique générale doit assurer un renouvellement d'air en permanence afin de limiter les risques pour la santé, en évitant l’accumulation de vapeurs nocives et explosives, par extraction et soufflage : l'air est transporté dans le local par un ventilateur de soufflage et extrait du local par un ventilateur d'évacuation. L’extraction de l'air se fait grâce à un système de collecte par ces ventilateurs, des gaines de diffusion, et un réseau de conduits qui captent et concentrent les poussières et vapeurs jusqu'aux filtres et aux épurateurs qui permettent de nettoyer l'air, puis de l’évacuer à l'extérieur par rejet dans l'atmosphère. La ventilation générale des ateliers doit être déterminée en fonction des aspirations locales pour ne pas perturber l’efficacité des captages à la source.
Les composants aérauliques comme les ventilateurs, les conduits entre autres doivent être accessibles et faciles d’entretien et de nettoyage. En particulier, les réseaux s’encrassent rapidement avec de filtres hors d’usage, une évacuation des condensats obstruée... - Une installation électrique conforme
L’incendie et/ou l’explosion peuvent provenir des équipements électriques, et en particulier, l’équipotentialité et la bonne mise à la terre de toutes les installations métalliques doivent être contrôlées, les prises défectueuses remplacées, il faut éviter toute accumulation d’électricité statique ....
Les étincelles, arcs et échauffements provoqués par les moteurs et appareillages électriques en fonctionnement peuvent aussi déclencher la catastrophe.
Il convient d’utiliser de l’appareillage électrique conçu pour atmosphères dangereuses afin de prévenir que le matériel, y compris l’éclairage, soit à l’origine d’un incendie ou d’une explosion.
Une métallisation au moyen d’un matériel conducteur et une mise à la terre appropriées de l'équipement de traitement et de manutention sont utiles pour dissiper et diriger à la terre en toute sécurité les charges électriques accumulées. La protection contre les contacts avec les masses mises accidentellement sous tension est obtenue par un dispositif de coupure automatique en cas de défaut d’isolement.
Dans les grandes installations, il est fortement recommandé de placer des explosimètres dans les zones de réception / manutention / stockage / expédition.
Dans le domaine des atmosphères explosives (Atex), des normes européennes fixent le cadre de travail des industriels et des installateurs. Depuis juin 2003, tout nouveau site de type Atex doit être équipé avec du matériel certifié, avec des enveloppes antidéflagrantes. Les autres installations doivent, depuis juin 2006, avoir été mises à niveau. - Un stockage des produits rigoureux
Le stockage des composants présente des risques tels que l’incendie, l’explosion, le risque de chute ou de renversement ou de détérioration d'emballage ... Toutes ces caractéristiques rendent nécessaire, outre les précautions lors de leur emploi, l’aménagement de locaux de stockage, avec des rayonnages métalliques, des planchers et des palettes normalisées. La réduction des risques existants passe par une réflexion sur la structure du local, sur les modalités de rangement et sur les incompatibilités entre les produits. Des procédures de stockage non adaptées peuvent entraîner une fragilisation des emballages à l'origine de fuites ou de ruptures accidentelles, de pollution, de réactions dangereuses ou d'accidents ou induire une modification ou une dégradation des produits qui le rendent plus dangereux car ils peuvent libérer des vapeurs inflammables ou nocives.
L’empilement doit être stable et sa hauteur ne doit pas affecter l’intégrité des emballages.
Le stockage des bidons de solvants, sacs, boites d’adjuvants ..., doit se faire dans un local ventilé par un système de ventilation mécanique, à l'abri de la chaleur et de l'humidité, et tous les conteneurs de produits chimiques doivent toujours être bien refermés.
L'installation électrique du local de stockage est à réaliser avec du matériel utilisable en atmosphère explosible.
Une bonne tenue des sols des locaux de stockage est essentielle pour éviter l’accumulation des matières déversées.
L’interdiction de fumer dans les locaux doit être absolument respectée et signalée de manière apparente (de même que toutes les autres consignes de sécurité).
Il faut stocker les plus faibles quantités de produits possibles car le risque d'incident ou d'accident croît avec la durée et le volume de stockage. - L’utilisation de machines et équipements adaptés
- La réduction des risques au cours des opérations d’impression 3D, notamment avec le procédé avec ABS, doit inclure une ventilation avec aspiration localisée.
- Systèmes d'encoffrement et de captage au plus près des émissions, de façon à évacuer les aérosols et les vapeurs :
Il convient de doter les installations de captages localisés et avoir des dispositifs de captage au dessus de l’ensemble des équipements (hottes aspirantes, plafonds filtrants ...), afin de maintenir un niveau d’exposition inférieur aux limites réglementaires. Dans le cas d’un capotage de l’imprimante, le filtre doit être adapté à la fois à la captation des particules (filtre HEPA) et à celle des COV (filtre à charbon) et on doit respecter sa durée d’utilisation.
- Des détecteurs de fumée pour repérer les surchauffes productrices d’émanations de décomposition thermique dangereuses.
- Dispositifs de sécurité des machines :
Toute machine doit porter les avertissements, signalisations et dispositifs d’alerte indispensables pour assurer la sécurité des travailleurs afin de supprimer ou réduire au minimum les risques de coupure, d’entraînement, d’écrasement, de cisaillement causés par les éléments exerçant une action directe sur la matière. Cette identification doit être réalisées par des pictogrammes et couleurs normalisées. Les éléments de travail doivent être disposés, protégés, commandés ou équipés de façon telle que les opérateurs ne puissent atteindre la zone dangereuse.
Les panneaux de signalisation seront choisis et disposés de façon à être perçus et compris facilement sans ambiguïté.
Chaque machine doit être munie d’un ou plusieurs dispositifs d’arrêt d’urgence clairement identifiables, accessibles et en nombre suffisant, permettant d’éviter les situations dangereuses en train de se produire.
- Le respect des recommandations des constructeurs et un entretien régulier des machines sont des éléments essentiels pour limiter les risques accidentels et pour prévenir des émanations. Ainsi l’utilisation et l'entretien des machines doivent être effectués par un personnel qualifié, spécifiquement formé (respect scrupuleux des capacités nominale des machines...) : de nombreux cas de fuites accidentelles peuvent survenir au niveau de différents équipements, ce qui entraîne la nécessité d’une maintenance rigoureuse des machines avec contrôle de l'étanchéité.
Des machines utilisées de manière non conforme ou mal entretenues et non vérifiées périodiquement créent un risque chimique supplémentaire. En particulier, les canalisations flexibles doivent être vérifiées périodiquement et remplacées en cas d’usure ou de choc, et en fonction de la durée maximale d’utilisation. - Un bon entretien des locaux
Une bonne tenue des locaux est essentielle pour éviter l’accumulation de déversements et de poussières sous ou autour des imprimantes. Les déversements peuvent créer un danger de glissement et par conséquent doivent être nettoyés immédiatement. De même, il convient de ramasser et enlever la poussière créée par les opérations de ponçage etc. - Le port d’équipements de protection individuel adéquat
Les équipements de protection individuelle sont nécessaires pour réduire le risque d’exposition non totalement éliminé par les mesures de protection collectives précédentes : masques respiratoires filtrants pour des travaux de courte durée (ponçage ...) ou dans des atmosphères polluées par des vapeurs de solvant organique et de résine, gants, vêtements de protection, chaussures et lunettes de sécurité.
Il s’avère indispensable de porter des gants de protection adaptés à la tâche effectuée et au produit manipulé : il n'existe pas de gant de protection universel. Le type de gants conseillé, imperméables, à longues manchettes, pour éviter la pénétration des produits à l’intérieur, doit être adapté aux différents produits manipulés selon leur composition qui figure sur la Fiche de Sécurité (par exemple gants de protection chimique en Viton ®). Le port des gants est obligatoire lorsque l’étiquetage du produit à manipuler comporte les phrases de risque R27 (très toxique par contact avec la peau), R24 (toxique par contact avec la peau), R21 (nocif par contact avec la peau), R34 (provoque des brûlures) et R35 (provoque de graves brûlures). - Le respect des règles d’hygiène et de sécurité
Des lavabos, postes de rinçage oculaire et des douches de sécurité doivent se trouver à proximité des postes de travail. Celles-ci permettent les mesures d'hygiène générale : lavage des mains fréquent avec lave-mains à commande non manuelle (au genou, au coude, électronique), douche en fin de poste... En effet, le respect des règles d’hygiène s’étend aux comportements individuels : ne pas avoir les mains sales afin de ne pas ingérer par inadvertance un produit toxique et ne pas manger sur le lieu de travail.
Le contact répété des solvants avec la peau entraînant un dessèchement cutané prédisposant aux dermatoses : aussi, il convient, pour l’hygiène des mains, de se laver les mains et les avant-bras après le travail et avant de manger en utilisant un savon adapté et/ou une fontaine de dégraissage et sans jamais utiliser de solvant organique comme détachant.
Le personnel doit avoir à sa disposition des vestiaires et des sanitaires correctement équipés et en nombre suffisant. Des vestiaires doubles doivent être mis à la disposition des travailleurs : l’entreposage des tenues de travail doit avoir lieu à l’abri de la poussière et des souillures (le rangement des tenues de ville et des tenues de travail doit être séparé).
Les consignes en cas d'accident (n° d'appel d'urgence, conduite à tenir, identification des services de secours) doivent être visiblement affichées.
Une trousse contenant le matériel de premiers secours non périmé doit être mise à la disposition du personnel, toute blessure cutanée doit immédiatement être désinfectée et pansée. Une projection oculaire de résine est une urgence ophtalmologique.
Des extincteurs doivent être disponibles en nombre suffisant et vérifiés annuellement. - La formation et l’information du personnel
La formation, par un organisme agréé, sur les dangers des produits utilisés et sur les moyens de se protéger, est indispensable : par exemple, comprendre les étiquettes du contenant des produits, lire les fiches de données de sécurité afin d’identifier les dangers des filaments dans les conditions du process ainsi que les moyens de protection à mettre en œuvre, connaître l’attitude à adopter en cas de fuite ou de déversement accidentel, savoir utiliser les E.P.I adéquats, formation aux premiers secours et incendie...
JUIN 2017
Partagez et diffusez ce dossier
Laissez un commentaire
Votre adresse de messagerie ne sera pas publiée.
Les avis des internautes
07/09/2023
Ces dossiers pourraient vous intéresser
Identification HSE
Créer mon compteNos rubriques
- Livres et édition
- Fiches Métier
- Materiel pédagogique
- Conseils
- Réparation matériels ATEX
- Travail en hauteur
- Sauveteur Secouriste du Travail (SST)
- Risque chimique
- Sécurité BTP
- Habilitations électriques
- Port des EPI
- Incendie - Explosion
- Gestes et postures - PRAP
- Conduite d'engins
- Prévention routière
- Formation continue à la sécurité
- Formation initiale à la sécurité
- Experts agréés auprés des CSSCT
- Formation de la CSSCT