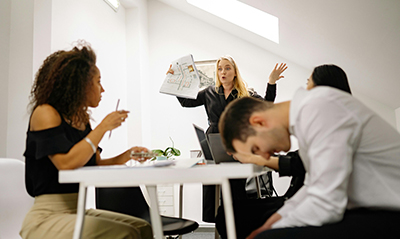
- Accueil
- Organisation Ergonomie
- Psychologie du travail
- Les risques organisationnels du Lean Management sur la santé au travail
Différentes méthodes de gestion industrielle, regroupées sous le terme de « Lean Management», sont apparues en france à la fin du XXème siècle (automobile, aéronautique..), puis se sont diffusées plus largement et sont mises en œuvre désormais dans de nombreux secteurs manufacturiers et même dans les activités du secteur tertiaire (services informatiques, bancaires, hospitaliers…). Le Lean Management cherche à améliorer les processus et vise une augmentation de la productivité par réduction des couts et des délais et une amélioration de la satisfaction au travail par développement de l'autonomie et de la participation du personnel. Mais le Lean Management peut aussi détériorer les conditions de travail si elles sont mal mises en œuvre : l'intensification du rythme de travail et de charge mentale sans réelles marges de manœuvre aboutit alors à une recrudescence de troubles musculo-squelettiques et de risques psychosociaux.
Différentes méthodes de gestion industrielle, regroupées sous le terme de « Lean Manufacturing » ou « gestion de production au plus juste », apparues au Japon puis théorisées et complétés aux Etats-Unis dans les années 80, sont apparues dans les processus de fabrication de grands groupes industriels français à la fin du XXème siècle (automobile, aéronautique..), puis se sont diffusées plus largement et sont mises en œuvre désormais dans de nombreux secteurs manufacturiers et même dans les activités du secteur tertiaire (services informatiques, bancaires, hospitaliers…) avec le « Lean Office » pour améliorer la performance administrative.
Le Lean Manufacturing cherche à améliorer les processus de fabrication de manière continue en supprimant tous les types d'actes superflus et de gaspillages (stocks, attentes, défauts, …) et tous les mouvements de pièces, gestes et taches inutiles par des gestions en flux tendus et en sollicitant la réactivité, la polyvalence et la flexibilité des opérateurs qui sont amenés à s'impliquer dans l'élimination des "non-valeurs ajoutées". Quant au Lean Office, l'idée est de considérer un bureau comme une usine ou la production est administrative (factures, contrats, commandes, travaux comptables…) et à y transposer l'application des pratiques du Lean Manufacturing.
Augmentation de la productivité par réduction des couts et des délais et amélioration de la satisfaction au travail par développement de l'autonomie et de la participation du personnel, le Lean Management peut aussi détériorer les conditions de travail si elles sont mal mises en œuvre, appliquées de manière directive, sans concertation, par un changement brutal : l'intensification du rythme de travail et de charge mentale sans réelles marges de manœuvre aboutit alors à une recrudescence de troubles musculo-squelettiques et de risques psychosociaux
Les caractéristiques des méthodes de Lean Management
Les méthodes du Lean Manufacturing sont à la fois des techniques de gestion industrielle et des techniques de gestion des ressources humaines : elles s'articulent autour de schémas productifs et d'attitudes managériales caractéristiques, développées initialement dans le Toyota Production System (TPS) et symbolisées par le slogan des 5 zéros (zéro stock, zéro délai, zéro défaut, zéro panne, zéro papier) et par le « kaisen », une démarche participative et continue d'amélioration de la productivité et de la qualité.
• Une technique de gestion industrielle en « flux tirés »
Elle vise une réduction drastique des stocks et une flexibilité de la production en fonction de ce que l'on a vendu, par opposition à la traditionnelle méthode en « flux poussés » où la production est établie en fonction de ce qu'on prévoit de vendre.
La procédure MRP (Material Requirement Planning) à la base de la technique des « flux poussés » pour les fabrications de produits standardisés est une méthode de calcul des besoins en composants et main d'œuvre fondée sur les nomenclatures des produits, les prévisions des ventes, les délais de fabrication ou d'approvisionnement et sur l'état des stocks permettant de passer des besoins bruts aux besoins nets : cela permet de gérer de façon automatique les sorties de stocks des pièces détachées ou de matières et les lancements des ordres de fabrication, en se réajustant périodiquement sur la demande effective avec des paramètres de gestion de stock pour le calcul du point de commande et de la quantité à commander. Les notions de stockage (dont le stock de sécurité) et d'automaticité font donc partie intégrante de la méthode MRP. En flux poussés, l'absence d'adaptation rapide aux variations de la demande, aux changements de série provoque soit des surstocks avec une immobilisation inutile de capitaux soit des ruptures avec un allongement des délais de livraison.
Le Lean Manufacturing propose une méthode en flux tirés (ou tendus) avec une organisation plus légère, plus réactive avec une production « juste à temps » (ou Just In Time) dans laquelle la fabrication d'une pièce est lancée pour satisfaire un besoin déjà existant, visant ainsi à diminuer les besoins en fond de roulement en réduisant les stocks et les en-cours et les frais financiers induits et à diminuer les délais de livraison des commandes en réduisant le cycle de fabrication : l'accélération de la rotation des capitaux employés aboutit à une amélioration conséquente de la rentabilité des investissements. Cette méthode met par contre le processus de production en tension, avec nécessité de gérer les aléas de production rapidement au fur et à mesure qu´ils apparaissent puisqu'il n'y a pas de stocks tampons, et exige de fortes capacités de réactivité et d'adaptation de la part des opérateurs, avec l'aide d'une série de signaux visuels sur des cartes et tableaux (kanban). Elle suppose aussi que la chaine logistique, celle des fournisseurs, sous-traitants s'adapte à cette méthode, donc établir une relation partenariale approfondie. On vise à obtenir un « standard », c'est à dire à généraliser les meilleures pratiques dans des procédures normalisées, connues et acceptées de tous les acteurs.
• Une attitude managériale basée sur la participation des opérateurs
Le Lean Manufacturing est aussi un mode de management basé sur la mobilisation des opérateurs pour rechercher l'efficacité dans la détection et la résolution de problèmes et pour développer une amélioration continue des performances en créant un état d'esprit cherchant à supprimer tous les types de gaspillages : surproduction, surstocks, attentes ou temps morts, manutentions et gestes inutiles, défauts de qualité. La démarche d'amélioration continue (kaisen) est un processus d'améliorations concrètes, simples, suggérées par chaque travailleur sur son lieu de travail, discutées en groupe, encouragé par un programme de motivation et une implication active du management avec des décisions adoptées par consensus. L'application de ces principes managériaux, résolution des problèmes au plus près du terrain impliquant les opérateurs tout autant que les responsables, laisse une autonomie dans la prise d'initiatives, essentielle en particulier dans la gestion « juste à temps » : le Lean Manufacturing associe les opérateurs pour stimuler l'innovation en leur donnant la possibilité d'exprimer leurs idées pour améliorer les processus de fabrication en productivité, qualité, sécurité ainsi que les conditions de travail. Le responsable hiérarchique et les travailleurs se retrouvent ainsi souvent dans des réunions de progrès ou de qualité (généralement hebdomadaire ou à la demande) pour réfléchir ensemble de manière consensuelle à la recherche permanente de l'excellence. C'est ce qui oppose le plus clairement le Lean Manufacturing aux méthodes utilisées dans les organisations tayloriennes de production (séparation entre la réflexion et l'exécution du travail, à la suite d'une analyse scientifique des différentes étapes du processus de production et définition des tâches précise et quantifiée).
La prévention des risques des méthodes de Lean Management
Le Lean Manufacturing, par lui-même, produit une intensification du travail, des sur-sollicitations physiques par élimination des temps d'attente et des déplacements jugés inutiles, alors que bien souvent ils permettent une récupération physique, et des contraintes cognitives par augmentation du nombre de tâches mentales. La pression sur les opérateurs pour traiter les aléas en urgence, pour augmenter la flexibilité de la production crée de plus des situations stressantes.
Néanmoins, une organisation de type toyotiste, qui laisse plus de place à l'initiative et à la participation, peut permettre à l'opérateur de devenir satisfait de son travail alors d'une organisation qui ne permet aucune marge de manœuvre (de type taylorienne) va interdire toute adaptation et laisser insatisfait ou malheureux le travailleur.
Il est clair aussi que le modèle de gestion du taylorisme, qui souligne comme uniques facteurs de motivation le salaire (la carotte, par la prime au rendement notamment), et la peur de la sanction répressive en cas d'indiscipline ou d'insuffisance (le bâton) a des effets pervers comme les défauts de qualité cachés et que le manque d'autonomie (et contrôle tatillon) de ce type de management est un facteur de souffrance psychique plus important que le toyotisme.
La jouissance d'autonomie et de responsabilité au niveau de celle que l'on est capable d'assumer est ainsi de nature à améliorer la motivation et la satisfaction au travail des opérateurs dans une organisation toyotiste bien conçue, malgré un renforcement de la charge mentale par ailleurs : mais, de fait, les méthodes du Lean Manufacturing sont souvent dévoyées dans les entreprises avec une application partielle, en ne gardant que l'aspect technique et productiviste et en oubliant les aspects psychologiques, ou en les instrumentalisant. Or, tout autant que les aspects techniques, les dimensions culturelles et managériales d'une adoption du Lean Manufacturing doivent absolument être prises en compte pour assurer l'amélioration à la fois des performances et des conditions de travail.
De plus, beaucoup de décisions de mise en œuvre du Lean Manufacturing privilégient une démarche de réalisation de changement radical et rapide (« kaisen blitz »), ce qui est contraire à l'esprit du « kaisen » du TPS, en négligeant la compréhension et l'appropriation par les acteurs qui auront à les mettre en œuvre, d'où anxiété, sentiment de perte des repères, de savoir-faire ou de pouvoir. Le déploiement massif et incontrôlé de systèmes de Lean Management fondés sur une rationalisation abusive des moyens, une augmentation excessive des contraintes organisationnelles temporelles, une exigence trop forte de réactivité et de flexibilité individuelle, une participation illusoire ou manipulatrice aux décisions, présente des risques de pénibilité physique (troubles musculo-squelettiques de gestes rapides et répétitifs sans temps mort) et de surcharge mentale (troubles psychosomatiques du stress, sur-engagement dans le travail, sentiment d'instrumentalisation).
La prévention des risques liés au Lean Manufacturing ou au Lean Office passe par une démarche ergonomique préalable et continue, une conduite du changement et une modification et adaptation profonde des styles de management.
• La démarche ergonomique
La mise en place d'un Lean Manufacturing commence par la méthode « 5S » (débarrasser, ranger, nettoyer, organiser et pérenniser) pour optimiser les postes de travail.
Si le « kaisen » est une démarche graduelle et douce, avec amélioration continue du système tenant compte des suggestions des opérateurs, cette unique approche minimaliste peut déboucher sur des postes de travail en réalité mal conçus sur un plan ergonomique : développer un nouveau processus de fabrication, de nouveaux postes et de nouvelles implantations et instructions de travail, suppose de recourir à des techniques issues de l'ergonomie, avec une étude en particulier des interfaces hommes-machines, des limites physiologiques...
Puis, lors du suivi de la méthode du Lean Manufacturing d'amélioration des postes de travail, il convient de disposer d'assez de personnes compétentes en organisation du travail pour traiter les problèmes remontés de la base, et d'associer les méthodistes, les ergonomes et la médecine du travail pour éviter les erreurs et utiliser leur possibilité d'intervention experte. L'adaptation des nouveaux modes opératoires aux différentes morphologies et capacités selon l'âge sont particulièrement à prendre en compte.
Il faut éviter que la quantification de toutes les tâches (chronométrage) n'aboutisse à la suppression intégrale de tous les moments d'échanges et de déplacements nécessaires au lien social et que les outils d'autocontrôle conduisent à un plus grand isolement du travailleur.
• La conduite du changement
L'application des principes du Lean Management impose de profonds changements dans les organisations industrielles ou tertiaires, avec des transformations importantes des postes et méthodes de travail, une véritable rupture, car il y a remise en cause de la manière d'agir des acteurs concernés.
D'où l'intérêt d'accompagner le changement par une démarche globale et participative au niveau de l'entreprise, de ses managers et du personnel : c'est ainsi que l'entreprise peut faciliter l'acceptation des changements et réduire les facteurs de rejet. En effet, pour les salariés, ce changement parait le plus souvent imposé par la direction et il convient alors de gérer les résistances naturelles qui s'opèrent. Les routines, les relations hiérarchiques s'érigent en systèmes de valeurs que menace cette réorganisation. Les réactions de résistance à l'égard du changement s'expliquent par le fait que les opérateurs doivent quitter leurs zones de confort apparentes et s'aventurer vers de nouveaux contextes de travail, de nouvelles tâches et responsabilités, mobiliser de nouvelles compétences, apprendre de nouveaux comportements, adopter de nouvelles attitudes et, surtout, abandonner leurs habitudes. Si les conditions de travail privilégiaient jusqu'à présent la spécialisation des taches alors qu'on évolue vers plus de polyvalence et de flexibilité, que la nouvelle démarche de qualité suppose des contrôles par l'opérateur lui-même alors qu'il en était déchargé jusqu'alors,… les obstacles au changement s'accroissent, et il faut prévoir une formation sérieuse pour pallier les difficultés d'adaptation.
- La consultation du CHSCT
Depuis la loi de modernisation sociale de janvier 2002, les prérogatives du CHSCT s'étendent à tous les domaines concernant la sécurité et la protection de la santé physique et mentale des salariés : ce qui englobe aussi l'aspect organisationnel pour laquelle l'instance doit être consultée. Le Comité d'Hygiène, de Sécurité et des Conditions de Travail a le droit d'avoir recours à une expertise externe en cas de projet important modifiant les conditions d hygiène et de sécurité ou les conditions de travail, afin de lui permettre d'avancer des propositions de prévention.
- La conduite du projet de Lean Management
La compréhension et l'acceptation par les salariés des nouvelles règles du jeu résultant du processus de changement passe par une conduite du projet qui :
- associe les personnes concernées dès le début du projet, afin notamment de prendre en compte leur avis et faire en sorte de le faire évoluer dans un sens favorable si nécessaire,
- met en place un dispositif de communication permettant tout au long du projet de permettre aux acteurs de l'entreprise de comprendre et d'accepter les changements à venir, ainsi que d'être informé sur l'avancement du projet,
- s'assure que les utilisateurs aient acquis les connaissances théoriques et pratiques nécessaires, par une formation sur les nouvelles méthodes de fabrication ou procédures administratives.
De nombreux projets de Lean Management peuvent être considérés comme des échecs. Les raisons d'échec vont du projet abandonné suite à de violentes réactions des salariés (ou de leurs chefs !), aux nouveaux systèmes ou applications mal ou sous utilisés, à la non-adhésion des utilisateurs entrainant retards et surcoûts de mise en œuvre, ... : la qualité du processus de mise en œuvre du changement est aussi importante que la qualité intrinsèque du changement proposé, et le facteur humain représente une des principales causes d'échec des projets de Lean Management.
Les entreprises de services sont les plus exposées aux difficultés d'implantation d'un Lean Office, car les salariés n'y sont pas culturellement préparés à une organisation scientifique du travail et peuvent ressentir une perte du sens du travail bien fait au profit d'un travail vite fait, une division plus grande du travail dévalorisante, une instrumentalisation exclusivement technique des contributions, conduisant à une véritable souffrance au travail et éventuellement à une hyperactivité professionnelle pour tenir le rythme.
Différentes démarches et pratiques de conduite de changement peuvent être utilisées, du type « gestion de projet », qui vont du diagnostic de la capacité au changement, à la communication jusqu'à la formation/coaching, valorisant le travail en groupe avec le type de résistances analysées au préalable : c'est le résultat d'un processus de réingénierie participative, non brutale et non directive. Il s'agit de constituer une équipe pluridisciplinaire et motivée disposant d'aptitudes et de compétences à gérer le processus de changement sur toute sa durée : capacité de travail en groupe, degré de maîtrise de la culture de management de projet, capacité d'animation et surtout de négociation ...
La constitution de l'équipe de conduite du changement peut se faire uniquement avec des ressources internes mais le recours à des prestataires externes est souvent nécessaire car les ressources externes peuvent être un gage d'objectivité et de neutralité, et elles disposent de compétences, de méthodes, techniques de communication expérimentées que n'ont pas les ressources internes. Un réseau interne de « correspondants du changement » est indispensable pour la réalisation en profondeur des actions de changement. Il représente la proximité qui est un facteur clé de réussite du changement. Il possède une bonne connaissance de l'existant, il permet d'avoir une bonne perception des différents freins, il peut identifier les bons interlocuteurs. Pour constituer ce réseau, il faut privilégier des acteurs reconnus professionnellement au sein des équipes.
L'implication et la participation des personnes dans la démarche est un facteur clé de réussite, et c'est à la base du principe du Lean Management. La gestion des résistances au changement demande de créer des espaces de dialogue au cours du processus de changement pour favoriser la compréhension, l'implication, l'appropriation et construire une réelle capacité à changer de l'organisation.
L'accompagnement collectif, organisé avec les opérationnels, vise à les amener à définir l'impact du changement et les actions à mener, le résultat des réflexions doit être formalisé pour leur donner de l'importance. Convaincre de la nécessité de changer et de s'engager dans un processus de changement nécessite l'organisation de séminaires de mobilisation et/ou création d'ateliers de réflexion mettant en avant la situation problématique actuelle, les opportunités d'amélioration et surtout les avantages attendus pour les équipes. Ces démarches participatives privilégient le brainstorming, le travail en groupe et l'action collective et misent sur l'influence mutuelle entre les personnes. Une fois qu'un premier groupe de personnes adhère au projet, cela permet de faire adhérer l'ensemble des collaborateurs concernés : à ce titre, l'exemplarité d'un test de mise en œuvre réussi pour un atelier ou service pilote est fondamentale.
Les salariés doivent être capables de rattacher la nouvelle organisation, les nouveaux processus, … à la réalité de leur quotidien pour surmonter leurs réticences.
Si cette conduite du changement n'a pas été mise en œuvre ou n'a pas abouti à une bonne perception et acceptation des transformations des postes ou des relations de travail, du contenu, de la durée ou des cadences du travail, le CHSCT peut exprimer son besoin d'informations plus claires sur les organisations, sur les conditions de travail qui attendent les salariés après la restructuration, sur les charges de travail, sur l'aménagement des locaux, les changements d'horaires, les mobilités fonctionnelles ou géographiques, la formation à de nouvelles technologies notamment informatiques…et les conséquences de ces changements sur la santé, les conditions de travail, la sécurité et les perturbations de la vie sociale des salariés.
• L'évolution des styles de management
Le Lean Management ne peut avoir de succès que lorsqu'il s'insère dans une culture d'entreprise prête à une telle transformation : l'état d'esprit et les comportements des managers disposés à laisser leurs subordonnés s'exprimer et prendre des initiatives, leur qualité d'écoute, un climat de travail sain et pas seulement court-termiste sont indispensables pour un tel changement d'envergure. A défaut, il faut envisager de renouveler les structures hiérarchiques trop autoritaires, strictement attachées aux décisions par voie descendante (top-down) et totalement rétives à l'inverse (bottom-up).
L'efficacité dépend de l'implication initiale de la hiérarchie, mais aussi du suivi des idées : la démarche d'innovation participative doit s'accompagner de véritables débats et de retours, à la fois dans l'application des suggestions et dans un système de récompense pour éviter des démarches participatives ressenties comme biaisées ou manipulées, au terme d'une concertation tronquée dans un cadre contraint de discussion ne permettant le débat que sur des activités ponctuelles, avec une autonomie seulement en apparence et des décisions prétendument consensuelles.
Pour aller plus loin
Etude INRS ED 6144 : Lean manufacturing : quelle place pour la santé et la sécurité au travail
(52 pages)
Juin 2013
Partagez et diffusez ce dossier
Laissez un commentaire
Votre adresse de messagerie ne sera pas publiée.
Ces dossiers pourraient vous intéresser
Identification HSE
Créer mon compteNos rubriques
- Salons, Livres et Edition
- Malveillance
- Logiciels & applications de sécurité
- Ergonomie au poste de travail
- Risque électromagnétique
- Psychologie du travail
- Organismes agréés de contrôle
- Rayonnements
- Ventilation, aération, filtrage et appareils de contrôle d'atmosphère
- Sécurité pour appareils à pression
- Materiel de signalisation
- Signalétique
- Outils anti-coupures
- Risque biologique
- Risque chimique
- Risque éléctrique
- Manutentions
- Etiquetage produits dangereux
- Prévention des Chutes
- Document Unique
- Mise en conformité machines - Dispositifs de protection - Equipements de stockage